In the realm of CNC machining, efficiency and precision are paramount. Achieving these goals hinges on utilizing advanced tools and technologies. Four critical components that significantly impact CNC operations are USB I/O controllers, smart relays, Mach4 probing, and CNC tool setters. Each of these elements plays a unique role in streamlining processes, ensuring accuracy, and optimizing performance. This article delves into these components, explaining their functions and highlighting their importance in modern CNC machining. Whether you’re an industry veteran or a newcomer, understanding these technologies can elevate your machining capabilities to new heights.
Now, let’s dive deeper into each of these essential components, starting with the USB I/O controller.
USB I/O Controller: The Backbone of CNC Connectivity
In the intricate world of CNC machining, the USB I/O controller serves as a crucial interface between the machine and the computer. This powerful device facilitates seamless communication, enabling precise control over various machining operations. Understanding the functionality and benefits of a USB I/O controller is essential for anyone looking to optimize their CNC setup.
What is a USB I/O Controller?
A USB I/O controller, short for Universal Serial Bus Input/Output controller, is a device that connects a CNC machine to a computer via a USB interface. It manages the input and output signals, translating them into commands that the CNC machine can execute. This controller ensures that the machine receives accurate instructions from the software, leading to precise and efficient machining processes.
Benefits of Using a USB I/O Controller
- Enhanced Connectivity: The primary advantage of a USB I/O controller is its ability to provide reliable and fast communication between the CNC machine and the computer. This connectivity is crucial for executing complex machining tasks with high precision.
- Versatility: USB I/O controllers are compatible with a wide range of CNC machines and software, making them a versatile choice for various applications. This flexibility allows users to upgrade their systems without worrying about compatibility issues.
- Ease of Installation: Installing a USB I/O controller is straightforward, often requiring just a plug-and-play setup. This simplicity reduces downtime and allows users to quickly integrate the controller into their existing systems.
Applications of USB I/O Controllers in CNC Machining
In CNC machining, a USB I/O controller is used to manage various tasks, from controlling spindle speeds to managing tool changes. It plays a vital role in ensuring that the machine operates smoothly and efficiently. By providing real-time feedback and precise control, the USB I/O controller helps in maintaining the accuracy and quality of the machined parts.
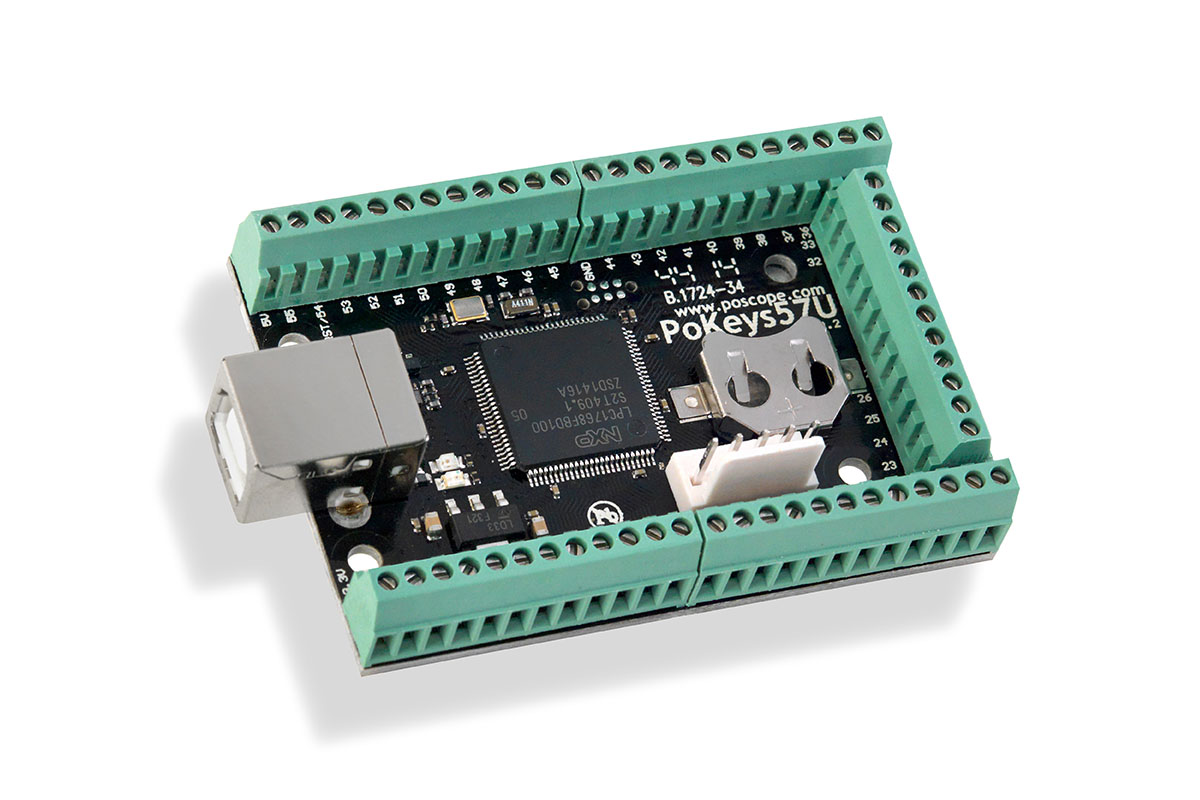
In conclusion, the USB I/O controller is a fundamental component in CNC machining, offering enhanced connectivity, versatility, and ease of installation. Its ability to manage complex machining tasks efficiently makes it an indispensable tool for any CNC operator. As we move forward, we’ll explore another crucial component in the CNC landscape: the smart relay.
Smart Relay: Enhancing Automation in CNC Machining
Automation is a key driver of efficiency in CNC machining, and smart relays are at the forefront of this technological revolution. These intelligent devices not only simplify the control of electrical circuits but also bring advanced features that enhance the overall functionality and reliability of CNC systems. Understanding the role of smart relays can significantly improve the automation and efficiency of CNC operations.
What is a Smart Relay?
A smart relay is an advanced form of an electromechanical relay that integrates programmable logic control (PLC) capabilities. Unlike traditional relays, which merely open or close circuits, smart relays can be programmed to perform complex control functions. This makes them an essential component in modern CNC systems, where automation and precision are paramount.
Benefits of Using a Smart Relay
- Programmability: The most significant advantage of a smart relay is its programmability. Users can set specific conditions under which the relay will activate or deactivate, allowing for precise control over CNC processes. This programmability leads to enhanced automation, reducing the need for manual intervention.
- Reliability: Smart relays are designed to be highly reliable, with built-in diagnostics and error-checking features. This reliability ensures consistent performance and reduces the likelihood of system failures, which is crucial in maintaining high production standards.
- Compact Design: Despite their advanced capabilities, smart relays are often compact and easy to integrate into existing CNC systems. This compact design saves space and simplifies the overall layout of the control panel.
Applications of Smart Relays in CNC Machining
In CNC machining, smart relays are used to automate various tasks, such as controlling the start and stop functions of the machine, managing the coolant system, and handling safety interlocks. By automating these processes, smart relays help reduce human error, increase productivity, and ensure consistent quality in the manufactured parts.
For example, a smart relay can be programmed to monitor the temperature of a CNC machine and automatically shut it down if it exceeds a predefined threshold. This not only protects the machine from damage but also enhances operator safety. Additionally, smart relays can manage multiple inputs and outputs, coordinating complex operations that would be challenging to handle manually.
In summary, smart relays bring a new level of automation and reliability to CNC machining. Their programmability, reliability, and compact design make them invaluable tools for improving efficiency and precision in CNC operations. Next, we’ll delve into another critical aspect of CNC machining: Mach4 probing.
Mach4 Probing: Precision and Efficiency in CNC Machining
In the pursuit of precision and efficiency in CNC machining, Mach4 probing stands out as an indispensable tool. This advanced probing system, integrated with Mach4 CNC software, enhances the accuracy of machining operations, reduces setup times, and improves overall productivity. Understanding Mach4 probing and its benefits can significantly elevate the quality and efficiency of your CNC processes.
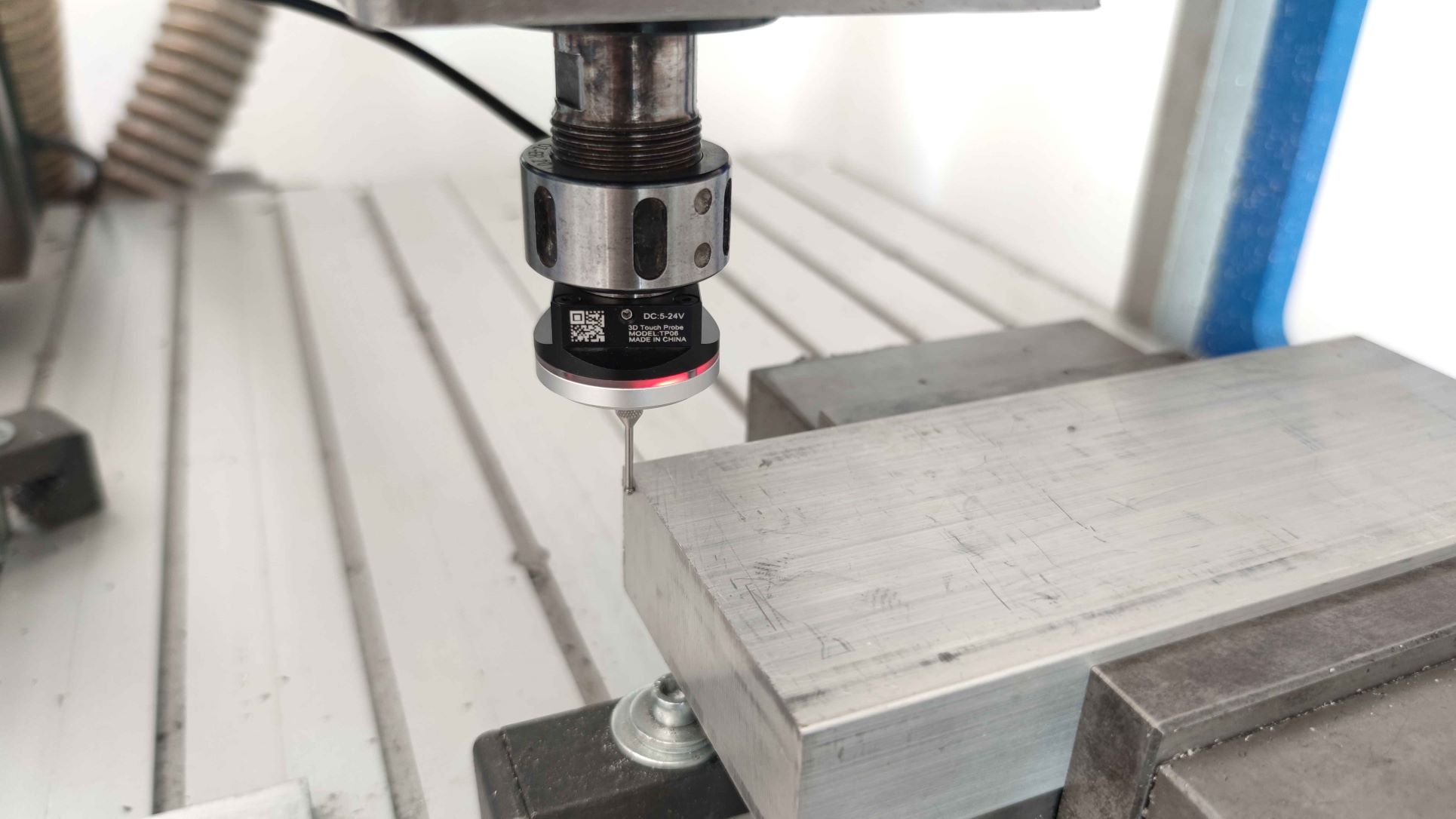
What is Mach4 Probing?
Mach4 probing is a sophisticated feature within the Mach4 CNC control software that uses a probe to accurately determine the position of a workpiece and its various features. The probe, typically attached to the CNC machine’s spindle, touches the workpiece at predefined points, allowing the software to map the exact coordinates and dimensions. This information is crucial for ensuring that the machining operations are precise and align with the design specifications.
Benefits of Using Mach4 Probing
- Increased Accuracy: One of the primary benefits of Mach4 probing is the significant increase in machining accuracy. By precisely determining the workpiece’s location and dimensions, the system minimizes errors and ensures that the final product meets the exact design requirements.
- Reduced Setup Time: Mach4 probing automates the setup process, drastically reducing the time required to align and position the workpiece. This reduction in setup time leads to higher productivity and allows operators to focus on other critical tasks.
- Enhanced Flexibility: Mach4 probing is highly flexible, capable of handling a wide range of workpiece shapes and sizes. This flexibility makes it suitable for various applications, from simple parts to complex geometries.
Applications of Mach4 Probing in CNC Machining
In CNC machining, Mach4 probing is used for several critical tasks, including workpiece setup, tool length measurement, and part inspection. These applications ensure that every stage of the machining process is accurate and efficient.
Workpiece Setup: By using Mach4 probing, operators can quickly and accurately determine the position of the workpiece. This setup process involves touching the probe to specific points on the workpiece, allowing the software to calculate its exact location and orientation. This precision ensures that subsequent machining operations are aligned correctly, reducing waste and improving quality.
Tool Length Measurement: Mach4 probing can also measure tool lengths, ensuring that the cutting tools are accurately positioned relative to the workpiece. This measurement is crucial for maintaining consistent machining depths and achieving the desired surface finish.
Part Inspection: After machining, Mach4 probing can inspect the final product to verify that it meets the design specifications. This inspection process involves probing various features of the machined part and comparing the measurements to the original design. Any discrepancies can be quickly identified and corrected, ensuring high-quality output.
In conclusion, Mach4 probing is a powerful tool that enhances the precision, efficiency, and flexibility of CNC machining operations. By automating critical tasks such as workpiece setup, tool length measurement, and part inspection, Mach4 probing ensures that CNC processes are accurate and productive. Next, we’ll explore the role of CNC tool setters in optimizing machining performance.
CNC Tool Setter: Optimizing Machining Performance
In the realm of CNC machining, achieving optimal performance hinges on the precise and efficient setting of cutting tools. The CNC tool setter is an essential device that facilitates this process, ensuring that tools are accurately calibrated and positioned. Understanding the role and benefits of a CNC tool setter can greatly enhance the quality and efficiency of your machining operations.
What is a CNC Tool Setter?
A CNC tool setter is a device used to measure and set the length and diameter of cutting tools with high precision. It typically involves a touch probe or laser system that interacts with the tool to determine its exact dimensions. This data is then used to adjust the tool offsets in the CNC machine, ensuring that each tool is correctly positioned for machining operations.
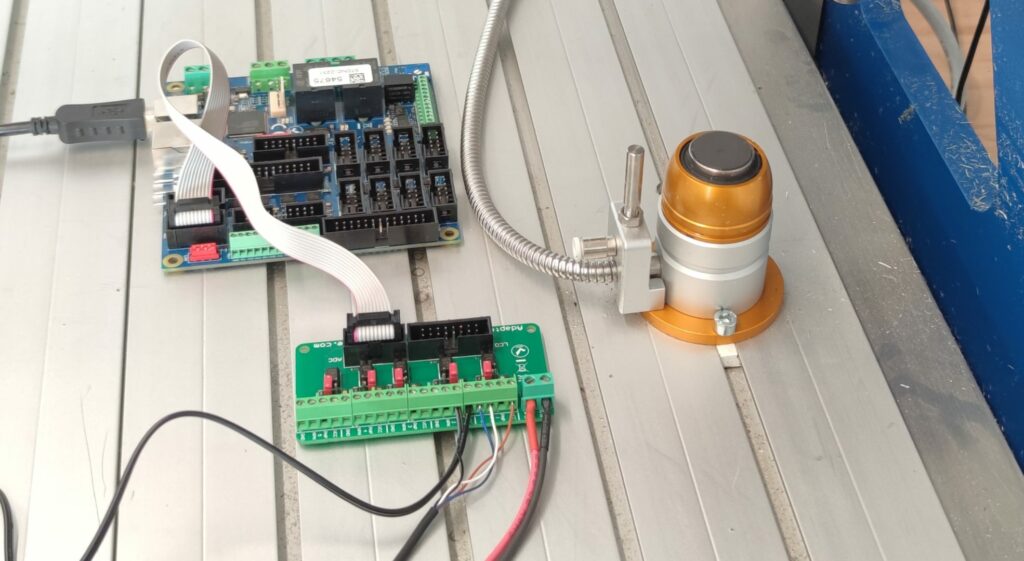
Benefits of Using a CNC Tool Setter
- Improved Precision: The primary benefit of a CNC tool setter is the significant improvement in machining precision. By accurately measuring tool dimensions, the tool setter ensures that each cutting tool is properly calibrated, reducing errors and enhancing the quality of the final product.
- Time Efficiency: CNC tool setters automate the tool measurement process, drastically reducing the time required for manual tool setting. This efficiency leads to increased productivity, allowing operators to focus on other critical tasks.
- Consistent Quality: By ensuring that tools are consistently set to the correct dimensions, CNC tool setters help maintain a high level of quality across multiple machining operations. This consistency is crucial for meeting stringent manufacturing standards and customer expectations.
Applications of CNC Tool Setters in CNC Machining
CNC tool setters are employed in various critical tasks within CNC machining, including tool length measurement, diameter calibration, and broken tool detection. These applications ensure that machining operations are efficient, accurate, and reliable.
Tool Length Measurement: One of the primary uses of a CNC tool setter is to measure the length of cutting tools. Accurate tool length measurement is essential for maintaining consistent cutting depths and achieving the desired surface finish. The tool setter touches the tool, measures its length, and automatically updates the CNC machine’s tool offset values, ensuring precise machining operations.
Diameter Calibration: CNC tool setters can also measure the diameter of cutting tools, ensuring that the tool’s width is accurately accounted for in the machining process. This calibration is crucial for operations requiring tight tolerances and precise cuts, such as in aerospace and automotive manufacturing.
Broken Tool Detection: Another important application of CNC tool setters is the detection of broken or worn tools. By regularly measuring the tools, the tool setter can identify any deviations from the expected dimensions, indicating potential tool damage. Early detection of broken tools prevents costly machining errors and reduces downtime associated with tool replacement.
In conclusion, CNC tool setters play a vital role in optimizing machining performance by improving precision, increasing time efficiency, and ensuring consistent quality. By automating the tool measurement process, CNC tool setters enhance the overall productivity and reliability of CNC operations. In the final section, we’ll summarize the key points covered and highlight how these technologies collectively enhance CNC machining.
Conclusion
The world of CNC machining is continually evolving, driven by advancements in technology that enhance precision, efficiency, and productivity. Four critical components that play a significant role in this evolution are USB I/O controllers, smart relays, Mach4 probing systems, and CNC tool setters. Each of these technologies brings unique benefits and applications to the CNC machining process.
The USB I/O controller serves as the backbone of CNC connectivity, ensuring seamless communication between the computer and the CNC machine. Its enhanced connectivity, versatility, and ease of installation make it an indispensable tool for managing complex machining tasks.
Smart relays bring a new level of automation and reliability to CNC systems. Their programmability, compact design, and robust performance help automate various processes, reducing human error and increasing productivity. They are essential for controlling electrical circuits and managing intricate CNC operations.
Mach4 probing enhances the accuracy and efficiency of CNC machining by providing precise workpiece setup, tool length measurement, and part inspection. This advanced probing system reduces setup time, increases machining precision, and ensures that the final products meet exact design specifications.
Finally, CNC tool setters optimize machining performance by accurately measuring and calibrating cutting tools. They improve precision, reduce setup times, and ensure consistent quality by automating the tool measurement process. Their applications in tool length measurement, diameter calibration, and broken tool detection are crucial for maintaining high standards in CNC machining.
In summary, the integration of USB I/O controllers, smart relays, Mach4 probing systems, and CNC tool setters can significantly elevate the capabilities of CNC machines. These technologies work together to enhance connectivity, automate processes, improve precision, and ensure consistent quality. By understanding and utilizing these advanced tools, CNC operators can achieve higher efficiency, reduced downtime, and superior machining outcomes. Embracing these innovations is key to staying competitive in the ever-evolving landscape of CNC machining.