In the realm of industrial automation, precision and control are paramount. Efficient operation and seamless integration of various components can significantly impact productivity and reliability. Among the critical components that play a vital role in this domain are Ethernet I/O controllers, USB stepper motor controllers, stepper motor driver manuals, and Modbus stepper drivers. These elements, each with their unique functionalities and applications, work together to enhance automation processes. In this article, we will delve into each of these components, exploring their significance, functionalities, and how they interconnect to form an integrated automation system. Whether you’re an engineer, technician, or enthusiast, understanding these components will provide you with valuable insights into the intricate world of industrial automation.
Ethernet I/O Controller
An Ethernet I/O controller is a crucial component in modern industrial automation systems. This device serves as a bridge between various input/output devices and a computer or network, facilitating efficient data communication and control over a network. Ethernet I/O controllers are widely used due to their ability to connect multiple devices over a standard Ethernet network, providing flexibility and scalability for automation systems.
One of the primary advantages of an Ethernet I/O controller is its high-speed data transfer capabilities. This speed is essential for real-time monitoring and control, ensuring that industrial processes run smoothly and efficiently. Moreover, the use of Ethernet networks allows for the integration of I/O devices with existing IT infrastructure, reducing the need for specialized cabling and simplifying the overall system architecture.
Ethernet I/O controllers also support a variety of communication protocols, such as Modbus TCP/IP, EtherNet/IP, and PROFINET. This compatibility makes them versatile and suitable for different industrial applications. For instance, in a manufacturing plant, an Ethernet I/O controller can be used to monitor and control machinery, manage production lines, and ensure safety protocols are adhered to, all through a single network interface.
Furthermore, these controllers are designed to be robust and reliable, capable of operating in harsh industrial environments. They often come with features such as redundant power inputs, wide operating temperature ranges, and rugged housings to withstand the demands of industrial use.
In summary, the Ethernet I/O controller is an indispensable component in industrial automation, offering high-speed communication, versatility, and reliability. Its ability to integrate seamlessly with various devices and networks makes it a cornerstone of efficient and scalable automation systems. Understanding its role and capabilities is essential for anyone involved in the design, implementation, or maintenance of industrial automation solutions.
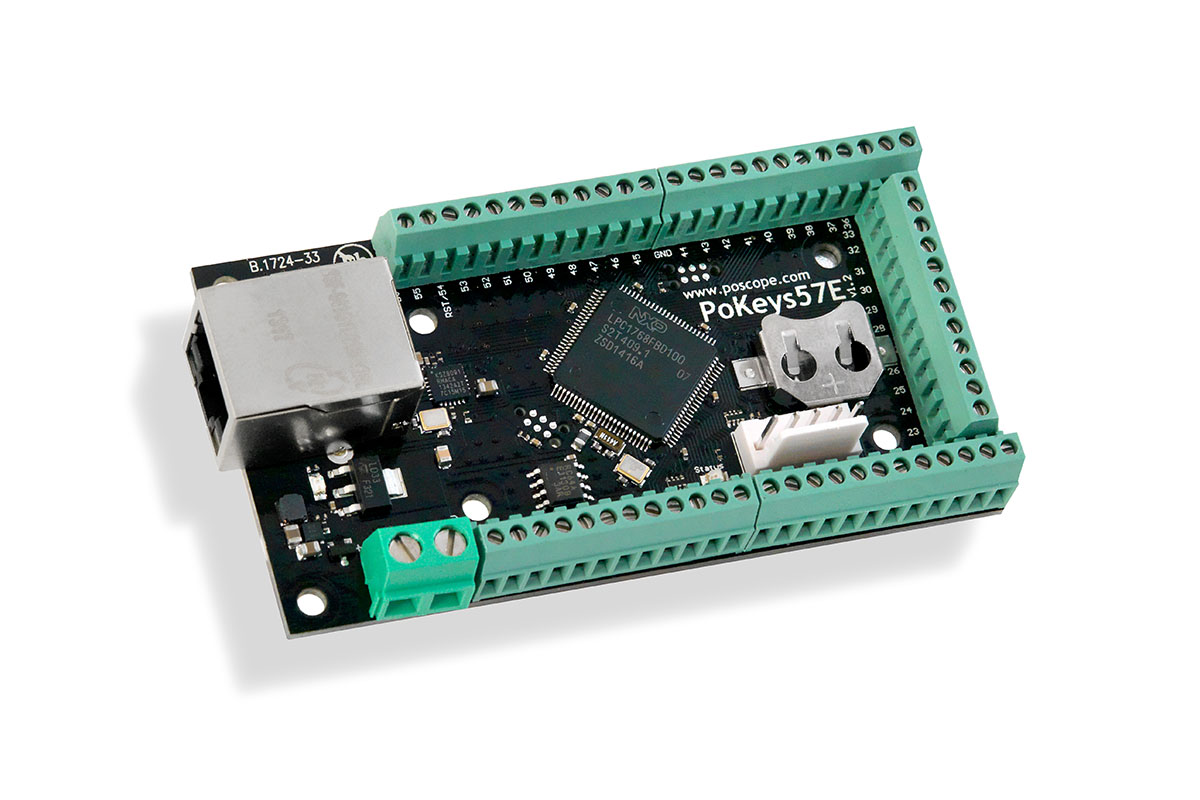
USB Stepper Motor Controller
The USB stepper motor controller is a pivotal device in the realm of precision motor control within industrial automation. This controller allows for the precise manipulation of stepper motors through a USB interface, making it an accessible and flexible solution for various applications. Its simplicity and ease of integration have made it a popular choice for both prototyping and production environments.
One of the primary benefits of a USB stepper motor controller is its straightforward connectivity. By leveraging the ubiquitous USB port, these controllers can easily connect to a wide range of computing devices, from desktop computers to embedded systems. This ease of connectivity facilitates rapid setup and configuration, which is particularly advantageous in development and testing phases.
Another key advantage of the USB stepper motor controller is its high level of control precision. Stepper motors are known for their ability to move in discrete steps, allowing for precise positioning and repeatability. The USB stepper motor controller enhances this precision by providing fine-tuned control over motor movement, speed, and direction. This precision is essential in applications such as CNC machines, 3D printers, and automated inspection systems, where accuracy is paramount.
In addition to precision, the USB stepper motor controller often includes software tools for easy configuration and programming. These tools typically feature graphical user interfaces that simplify the process of setting motor parameters, creating motion profiles, and implementing control algorithms. This user-friendly approach reduces the learning curve and enables users to quickly deploy and adjust their motor control solutions.
Moreover, USB stepper motor controllers are designed to be compact and portable. Their small footprint makes them ideal for applications with limited space or those requiring mobility. Despite their compact size, these controllers are powerful and capable of driving stepper motors in a variety of demanding industrial scenarios.
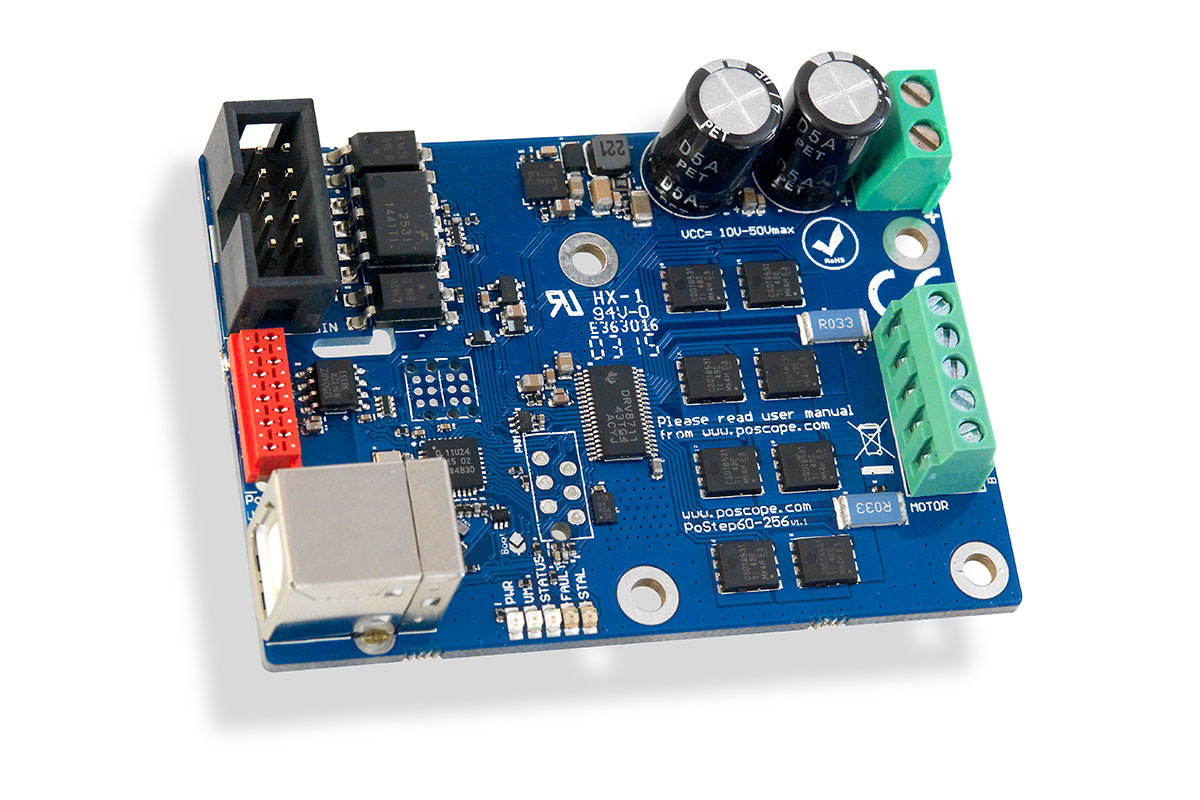
In summary, the USB stepper motor controller is a versatile and user-friendly device that provides precise control over stepper motors via a convenient USB interface. Its ease of connectivity, precision, and compact design make it a valuable tool in numerous industrial automation applications. Understanding its functionalities and advantages is crucial for anyone involved in motor control and automation projects.
Stepper Motor Driver Manual
A stepper motor driver manual is an essential resource for anyone involved in the installation, operation, and maintenance of stepper motor systems. This manual provides comprehensive guidance on how to effectively use a stepper motor driver, ensuring optimal performance and longevity of the motor and the overall system. Understanding the information within a stepper motor driver manual is crucial for both novices and experienced professionals in the field of industrial automation.
One of the primary sections of a stepper motor driver manual is the setup and installation guide. This section typically includes detailed instructions on how to connect the driver to the stepper motor, power supply, and control interfaces. It also outlines the necessary steps to configure the driver settings, such as current limits, microstepping modes, and other parameters. Proper setup is critical to ensure that the stepper motor operates efficiently and within its specified limits, preventing damage and ensuring reliable performance.
Another important aspect covered in a stepper motor driver manual is the operation and control instructions. This section explains how to send control signals to the driver, manage motor speed and direction, and implement various motion profiles. It often includes diagrams and example code snippets to help users understand the control mechanisms. Mastery of these control techniques allows for precise and accurate movement of the stepper motor, which is essential in applications like robotics, CNC machinery, and automated manufacturing processes.
The troubleshooting section of a stepper motor driver manual is equally vital. This section helps users diagnose and resolve common issues that may arise during the operation of the stepper motor driver. It provides solutions for problems such as motor stalling, overheating, and unexpected behavior. By following the troubleshooting guidelines, users can quickly identify and fix issues, minimizing downtime and maintaining productivity in their automation systems.
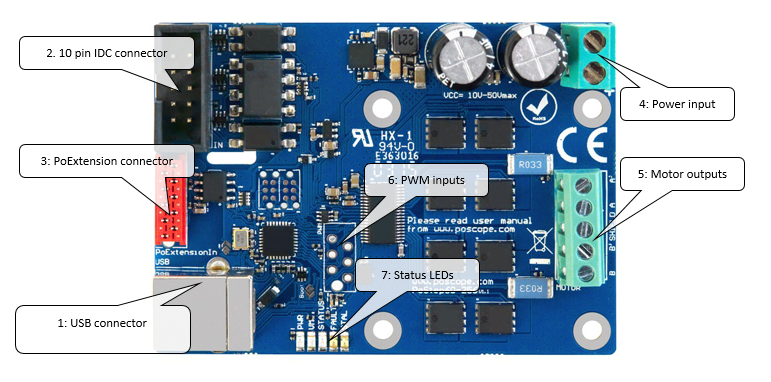
Safety precautions are another critical element found in a stepper motor driver manual. This section highlights the potential hazards associated with the use of stepper motor drivers and provides recommendations for safe handling and operation. Adhering to these safety guidelines is essential to protect both the user and the equipment from harm.
In summary, a stepper motor driver manual is an indispensable tool for anyone working with stepper motor systems. It provides detailed instructions for setup, operation, troubleshooting, and safety, ensuring that users can achieve optimal performance and reliability from their stepper motors. Familiarity with the contents of the stepper motor driver manual is essential for successful implementation and maintenance of stepper motor-driven automation systems.
Modbus Stepper Driver
A Modbus stepper driver is a specialized device that combines the capabilities of stepper motor control with the robust communication features of the Modbus protocol. This integration allows for efficient and precise control of stepper motors in various industrial automation applications. Understanding the functionalities and advantages of a Modbus stepper driver is essential for optimizing automation processes and ensuring seamless system integration.
The primary advantage of a Modbus stepper driver is its ability to communicate over the widely-used Modbus protocol. Modbus is a serial communication protocol commonly used in industrial environments for connecting various devices and transferring data. By utilizing Modbus, the stepper driver can be easily integrated into existing control systems, facilitating centralized control and monitoring of multiple devices. This connectivity enhances the overall efficiency and coordination of the automation system.
Another key benefit of a Modbus stepper driver is its precise motor control capabilities. These drivers are designed to offer fine-tuned control over the stepper motor’s movements, including speed, direction, and positioning. The Modbus protocol allows for real-time communication between the stepper driver and the control system, ensuring accurate and responsive motor control. This precision is particularly valuable in applications such as conveyor systems, robotic arms, and precision machining, where exact motor movements are critical.
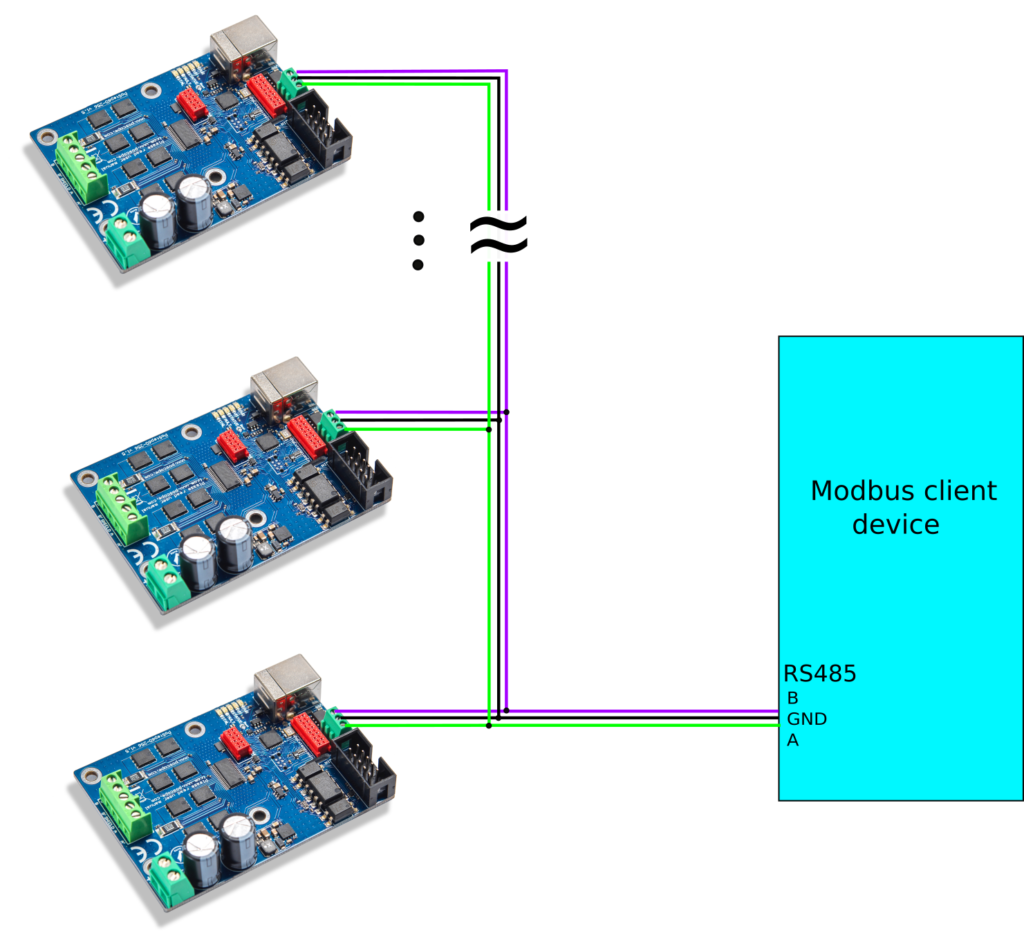
Modbus stepper drivers also support a range of advanced features that enhance their functionality and flexibility. These features may include configurable microstepping, current limiting, and acceleration/deceleration control. By adjusting these parameters, users can optimize the performance of the stepper motor for specific applications, achieving smoother and more efficient operation. Additionally, some Modbus stepper drivers offer diagnostic and monitoring capabilities, allowing users to track performance metrics and identify potential issues before they become critical.
Furthermore, the use of Modbus stepper drivers simplifies the overall system architecture. Since Modbus is a standardized protocol, it reduces the complexity of wiring and system configuration. This standardization also ensures compatibility with a wide range of industrial devices and control systems, making it easier to expand and modify the automation system as needed.
In summary, a Modbus stepper driver combines the precision of stepper motor control with the robust communication features of the Modbus protocol. This integration enables efficient and accurate motor control, seamless system integration, and advanced functionality for various industrial automation applications. Understanding the capabilities and benefits of Modbus stepper drivers is crucial for optimizing automation processes and achieving reliable and coordinated system performance.
Conclusion
In the intricate world of industrial automation, the seamless integration and precise control of various components are crucial for efficiency and reliability. The four key components discussed in this article—Ethernet I/O controllers, USB stepper motor controllers, stepper motor driver manuals, and Modbus stepper drivers—each play a vital role in achieving these goals.
The Ethernet I/O controller stands out for its ability to facilitate high-speed data transfer and communication over standard Ethernet networks. This capability allows for the integration of multiple devices, enhancing the scalability and flexibility of automation systems. Its support for various communication protocols and robust design makes it indispensable in industrial settings.
The USB stepper motor controller offers straightforward connectivity and precise control over stepper motors through a USB interface. Its user-friendly setup and configuration, coupled with high control precision, make it ideal for applications requiring accurate and repeatable motor movements, such as CNC machines and 3D printers.
A stepper motor driver manual is an essential resource for ensuring the proper installation, operation, and maintenance of stepper motor systems. It provides detailed instructions, troubleshooting tips, and safety guidelines that are crucial for achieving optimal performance and longevity of stepper motors in industrial applications.
Lastly, the Modbus stepper driver combines stepper motor control with the robust communication features of the Modbus protocol. This integration allows for efficient, centralized control and monitoring, enhancing the precision and coordination of automation processes. Its advanced features and standardization simplify system architecture and ensure compatibility with a wide range of industrial devices.
Together, these components form the backbone of modern industrial automation, providing the necessary tools and technologies for efficient, precise, and scalable operation. Understanding their functionalities and benefits is essential for anyone involved in the design, implementation, or maintenance of automation systems. By leveraging these components effectively, industries can achieve higher productivity, reliability, and operational excellence.