In the ever-evolving world of engineering and automation, precision and control are paramount. From the manufacturing of intricate parts to the seamless operation of model railways, technological innovations are continuously shaping the way we approach complex tasks. One of the cornerstones of this technological transformation is the CNC controller, which plays a pivotal role in ensuring accuracy and efficiency in various applications, including industrial machinery and hobbyist projects. Coupled with advanced systems like the PoKeys57U, these controllers enable real-time communication and refined control, further enhancing automation processes.
As automation extends its reach into diverse fields, industries and enthusiasts alike are discovering new possibilities. For instance, model railway automation is no longer a simple hobby but a sophisticated exercise in precision, requiring advanced tools to simulate real-world scenarios. Similarly, testing equipment like the slip ring test is vital in ensuring the longevity and functionality of rotating components used in machinery and various electrical systems.
This article delves into the significance of CNC controllers, with a special focus on the PoKeys57U, and explores their applications in model railway automation and slip ring testing. By examining each topic, we will understand how these technologies converge to provide greater precision, reliability, and automation across various domains.
The Role of CNC Controllers in Modern Engineering
In today’s fast-paced industrial landscape, the need for precision and automation is greater than ever before. One of the key technologies that have made this possible is the CNC controller. Standing for Computer Numerical Control, a CNC controller is the brain behind many modern manufacturing machines, such as lathes, milling machines, and 3D printers. These controllers allow machines to execute highly precise and complex movements, controlled by computer instructions, which are translated into exact movements of tools and parts.
The operation of a CNC controller is based on a set of commands that define the exact path a tool should follow to produce a specific component. This digital control enables the machining process to be automated, drastically improving efficiency and reducing the margin for human error. Whether in the aerospace, automotive, or medical industries, CNC controllers are at the heart of manufacturing processes that demand high precision and speed. They ensure that every part, no matter how small, meets the strictest quality standards.
One of the key advantages of CNC controllers is their ability to process complex geometries that would be impossible or highly inefficient to produce manually. The software used to program CNC machines can model intricate shapes, curves, and patterns, allowing manufacturers to produce parts with exceptional precision. In addition to this, CNC controllers offer repeatability — once a program is established, the machine can continuously produce identical parts, ensuring uniformity and reducing waste.
The flexibility of CNC controllers is another important factor in their widespread adoption. Different types of CNC controllers can be configured to work with a variety of machines, including milling machines, lathes, routers, and laser cutters. This versatility allows industries to optimize their production lines, saving both time and cost. Additionally, many modern CNC controllers come with advanced features such as touch-screen interfaces, real-time diagnostics, and integration with CAD/CAM systems, making them even more user-friendly and efficient.
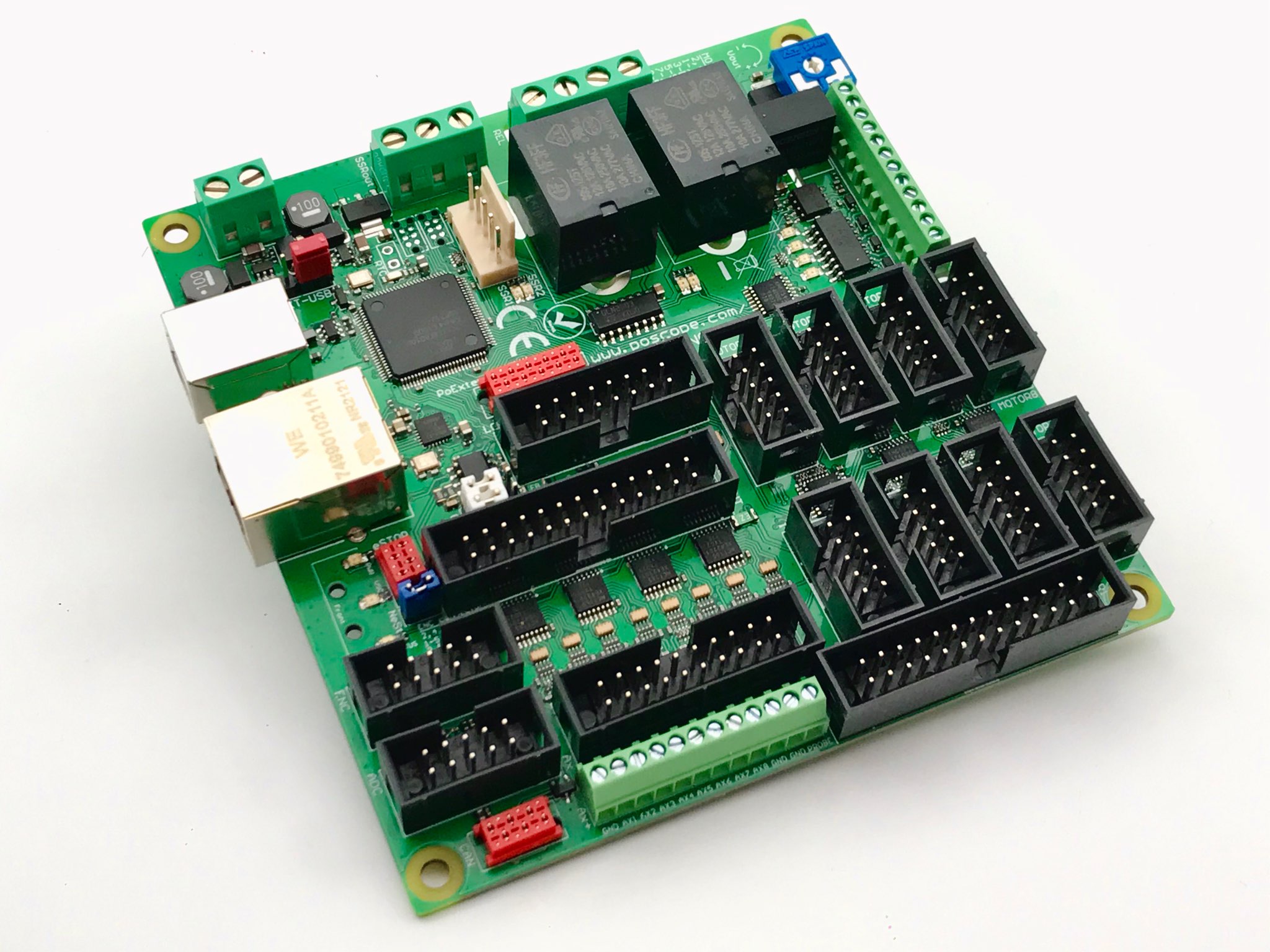
Despite the impressive capabilities of CNC controllers, there is always a need for continual innovation to keep up with evolving demands. As industries move toward more complex products and greater efficiency, newer controllers, like the PoKeys57U, have emerged to provide enhanced connectivity and automation. By integrating CNC controllers with systems like the PoKeys57U, manufacturers can extend the capabilities of their machines, enabling them to perform a wider range of tasks with greater precision and ease. This synergy between the CNC controller and advanced modules is revolutionizing industries, from small-scale workshops to large-scale production lines, making automation more accessible and powerful than ever before.
The role of CNC controllers in modern engineering cannot be overstated. Their ability to precisely control machines, automate processes, and enhance productivity has transformed industries and opened the door to new possibilities in manufacturing. However, as technology continues to advance, the integration of more sophisticated systems, such as the PoKeys57U, will play a crucial role in further elevating the capabilities of CNC-controlled machines. With their potential for greater precision, flexibility, and ease of use, these controllers will continue to be a cornerstone of modern engineering for years to come.
Exploring the PoKeys57U and Its Impact on Automation
The PoKeys57U is a versatile and powerful device that plays a critical role in enhancing automation systems across various industries. As part of the PoLabs product family, the PoKeys57U is a motion controller that integrates seamlessly with CNC controllers, expanding their capabilities and allowing for a higher level of precision and control. It provides a user-friendly interface for machine control, offering an array of advanced features that can be leveraged for a wide range of applications, from industrial automation to hobbyist projects.
At its core, the PoKeys57U is a USB-based device that allows for the integration of CNC machines with computers. It acts as an interface between the machine and the computer, providing real-time control over multiple axes and other machine components. The PoKeys57U is capable of supporting up to five stepper or servo motor drivers and can control up to 56 I/O devices, which makes it a powerful tool for controlling complex automation systems. It allows users to fine-tune settings for motion, speed, and torque, which makes it ideal for scenarios where precision is of utmost importance.
One of the standout features of the PoKeys57U is its built-in PoNET communication protocol, which allows multiple PoKeys devices to be connected and communicate with each other over a network. This networked setup enables users to expand their automation systems easily and efficiently. For example, multiple PoKeys57U units can be employed to control different parts of a larger production system, each communicating with others to coordinate complex tasks. This ability to scale up automation systems without sacrificing performance is a significant advantage for industries looking to optimize their operations.
The PoKeys57U is also known for its compatibility with popular CNC software like Mach3, Mach4, and LinuxCNC. This makes it an attractive choice for anyone already familiar with these software platforms. The PoKeys57U offers easy integration with these systems, providing a seamless experience for users. It supports multiple encoders, enabling high-precision feedback and ensuring that motion and positioning are executed with extreme accuracy. For industries such as robotics, electronics manufacturing, and even small-scale hobbyist applications like model railway automation, the PoKeys57U offers the necessary tools for sophisticated automation control.
Moreover, the PoKeys57U provides various I/O options, including digital and analog inputs and outputs, relays, and high-speed counters. This versatility allows it to control a wide range of devices, from simple on/off switches to more complex sensors and actuators. Its modular design also allows users to customize the system by adding extra I/O devices or modules as needed. This adaptability makes the PoKeys57U particularly useful in environments where frequent changes or upgrades to automation systems are required.
When integrated with a CNC controller, the PoKeys57U adds an additional layer of control and precision. For example, in a typical CNC machine setup, the CNC controller manages the primary motion and cutting functions, while the PoKeys57U can be used to manage secondary systems, such as cooling, lighting, or auxiliary machine operations. This division of labor between the two devices ensures that each part of the system operates efficiently and without interference, leading to more streamlined and effective workflows.
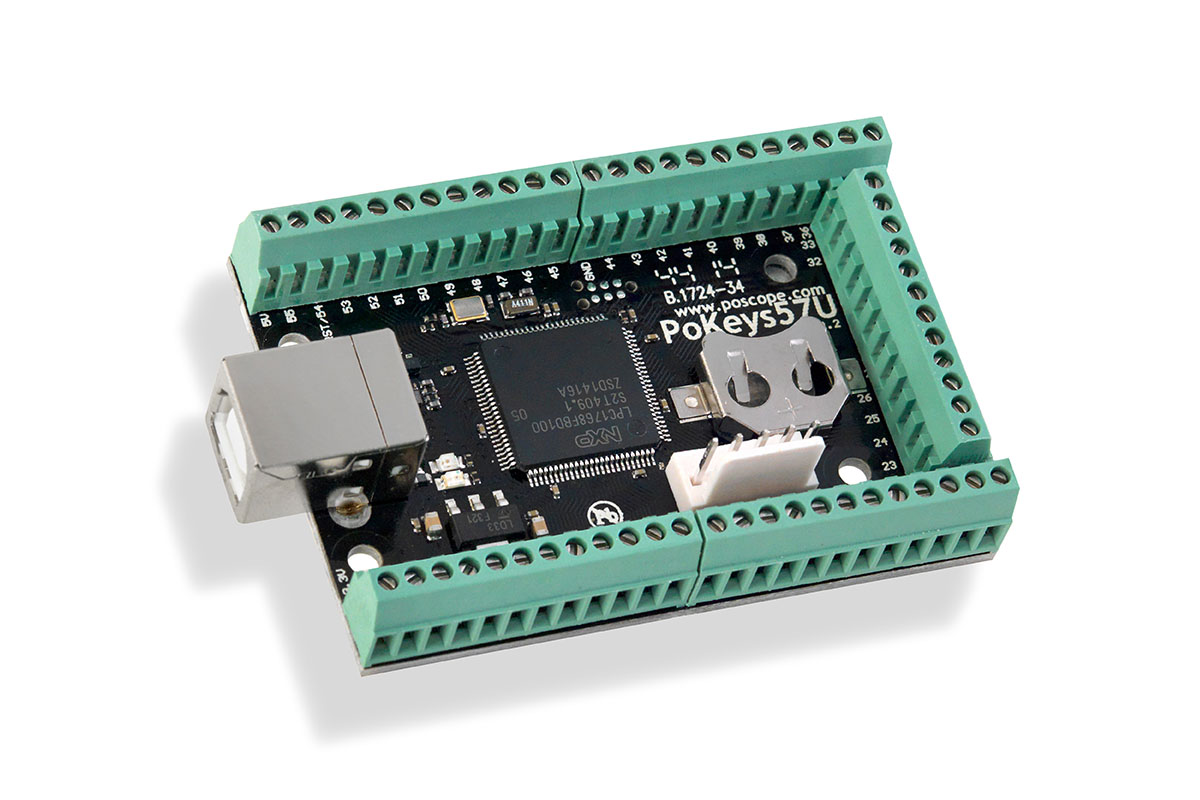
In the context of model railway automation, the PoKeys57U proves invaluable as well. Many model railway enthusiasts use CNC-controlled machines and automated systems to create lifelike scenarios, complete with moving trains, signals, and lighting. By incorporating the PoKeys57U into these setups, users can enhance the level of detail and realism by automating complex tasks such as controlling train speeds, switching tracks, and managing station lighting. This added level of control and automation takes model railroading to new heights, transforming it from a simple hobby into a sophisticated, interactive experience.
The PoKeys57U’s combination of versatility, precision, and scalability makes it an indispensable tool in the world of automation. Whether it’s controlling a CNC machine, managing a complex production system, or enhancing a model railway setup, the PoKeys57U provides the flexibility and power needed to handle a variety of tasks. Its ability to integrate with existing CNC controllers and other automation devices ensures that it remains at the forefront of technological advancements in both industrial and hobbyist sectors. As industries continue to push the boundaries of automation, the PoKeys57U will undoubtedly play a pivotal role in driving future innovations.
The Fascinating World of Model Railway Automation
Model railway automation has evolved from a simple pastime into a highly sophisticated field, blending engineering, electronics, and technology to create incredibly detailed and dynamic layouts. While traditional model railways were manually controlled, modern model railway automation systems integrate cutting-edge technology, including CNC controllers and devices like the PoKeys57U, to automate everything from train movement to station signaling, creating more realistic and interactive experiences. Automation in model railroading allows enthusiasts to simulate real-world train operations, transforming static displays into vibrant, moving ecosystems.
One of the most exciting aspects of model railway automation is the ability to control every aspect of the railway environment automatically, often with very little human intervention. For example, trains can be programmed to travel along preset tracks, stop at stations, switch lines, or change direction based on specific triggers. The addition of sensors, actuators, and controllers within the model railway system allows for highly detailed and lifelike movements. These systems often use CNC controllers to manage the motion of trains, control switches, and even activate scenery elements such as lights, gates, and automated signals.
The integration of a CNC controller in model railway automation systems allows enthusiasts to program the precise movements of trains along their tracks. A CNC controller works by taking computer-generated commands and translating them into specific actions—like moving a train from one station to another, or activating a signal. The CNC controller can be programmed to follow a fixed timetable or react dynamically to changes in the environment, such as the presence of another train on the same track. This level of precision is crucial for creating a realistic railway environment, where trains must not only run smoothly but also interact intelligently with one another.
One of the most valuable tools in modern model railway automation is the PoKeys57U. This device provides an intuitive and scalable solution for automating various components of a model railway system. For instance, it can control track switches, monitor train positions, and even adjust the speed of the trains. The PoKeys57U can be connected to various sensors placed throughout the model railway, allowing it to detect when trains approach certain points, triggering pre-programmed actions such as stopping the train at a station or switching tracks. This is an example of how automation in model railroads mirrors real-world train operations, where sensors detect approaching trains and adjust signals accordingly to ensure safety and efficiency.
Additionally, model railway automation can be enhanced by adding more complex systems, such as automated signals and station management. Using PoKeys57U, modelers can link different sections of the railway layout, allowing for multi-train operations, each with its own programmed schedule. The PoKeys57U provides the necessary interfaces for sensors, motor drivers, and I/O devices, all of which contribute to the seamless coordination of multiple trains running concurrently on the same layout. This level of integration and automation enables more engaging and realistic scenarios, with trains moving in and out of stations, crossing signals, and avoiding collisions, all while requiring minimal intervention from the operator.
The precision offered by CNC controllers and devices like the PoKeys57U is not just limited to controlling the trains themselves but extends to every detail of the railway environment. For example, automated lighting systems can be used to simulate day and night cycles, adjusting the brightness of the lights based on the time of day in the model railway’s virtual world. Automated gates and crossing signals can be synchronized to the movement of trains, ensuring they activate when a train is approaching and deactivate when it has passed. The combination of these automated elements, powered by CNC controllers and PoKeys57U, creates a dynamic and immersive model railway experience that rivals real-world train systems.
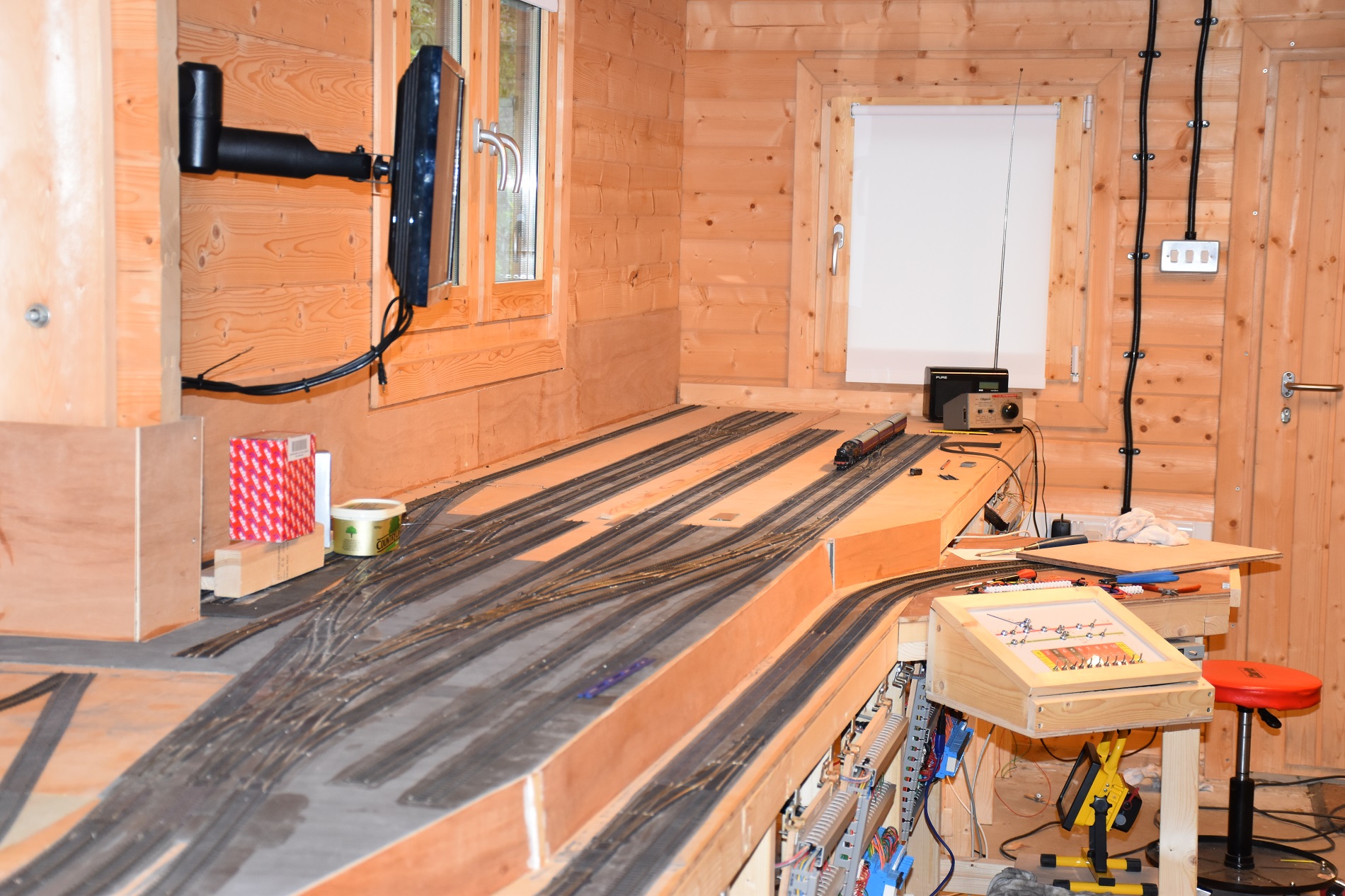
For enthusiasts, the joy of model railway automation lies in the ability to continually expand and refine their layouts. With the advancements in CNC controller technology and devices like the PoKeys57U, there is virtually no limit to the complexity of automation that can be integrated into a model railway system. From controlling individual trains to managing entire stations and complex track networks, automation allows for a level of precision and realism that was once unimaginable. The ability to automate a model railway layout is not only a fascinating challenge for hobbyists but also an invaluable learning experience, blending creativity with technical skills.
The impact of model railway automation extends beyond the hobbyist community. It provides valuable insights into the challenges and benefits of automation in real-world transportation systems. For example, understanding how to automate train schedules, manage multiple moving parts, and ensure safety protocols are in place can have applications in actual railway systems and other industries. Model railway enthusiasts often use their automated layouts as testing grounds for concepts that could later be applied to full-scale engineering projects.
In conclusion, model railway automation has transformed a simple hobby into a complex, interactive experience, thanks to technologies like CNC controllers and the PoKeys57U. These innovations have made it possible to create lifelike, automated systems that mimic the precision and coordination found in real-world train operations. As automation continues to advance, the world of model railroading will only become more immersive, offering endless possibilities for creativity and technological experimentation.
The Importance of Slip Ring Tests in Industrial Automation
In the realm of industrial automation and machinery, ensuring the longevity, efficiency, and reliability of rotating components is paramount. One critical aspect of maintaining these systems involves slip ring tests. A slip ring is an essential device that allows the transmission of electrical signals and power from a stationary part to a rotating part, enabling continuous motion without interruption. They are commonly used in machinery like wind turbines, industrial robots, CNC machines, and other automated systems where continuous rotation is required.
A slip ring test involves evaluating the performance and functionality of slip rings to ensure they can reliably carry current and data signals without causing power loss or degradation in the system. These tests are particularly vital in systems that rely heavily on continuous rotation, such as CNC machines, which often have rotating spindles that require uninterrupted power and signal transmission. If a slip ring fails or malfunctions, it can lead to costly downtime, inefficiency, and potential damage to sensitive equipment. Therefore, regular slip ring tests are crucial to avoid unexpected failures and to maintain the high performance expected from these advanced automation systems.
The main purpose of a slip ring test is to check for wear and tear, electrical continuity, and signal integrity over time. As slip rings rotate, friction and mechanical stress naturally cause wear, which can lead to electrical resistance or even failure. Regular testing helps identify signs of deterioration, allowing for early intervention before a malfunction occurs. These tests typically involve measuring the resistance across the slip ring’s brushes, verifying the smoothness of the rotation, and ensuring there is no interference or signal degradation in the transmission of power and data.
For CNC controllers and systems like the PoKeys57U, slip ring tests ensure that the rotating components responsible for motion and control are consistently operational. In CNC machinery, slip rings are commonly used in applications where a rotating tool or spindle needs a constant supply of power or data signals, such as in multi-axis motion control systems. A failure in the slip ring could result in erratic machine behavior, poor precision, or even total machine failure. By performing regular slip ring tests, operators can ensure that power and signal transmission remain stable, preventing disruptions in the highly precise operations that CNC controllers enable.
In addition to their importance in CNC machines, slip rings are also integral to other automated systems where rotational movement is involved. For instance, in industrial robotics, slip rings allow for continuous rotation of robotic arms while still transmitting power and control signals to perform tasks like welding, assembly, or inspection. Slip ring tests are essential in these systems to prevent power loss or communication errors that could lead to inaccuracies or equipment failure. Ensuring that the slip rings are in optimal condition is vital to the reliability of robotic automation in industries like manufacturing, aerospace, and automotive production.
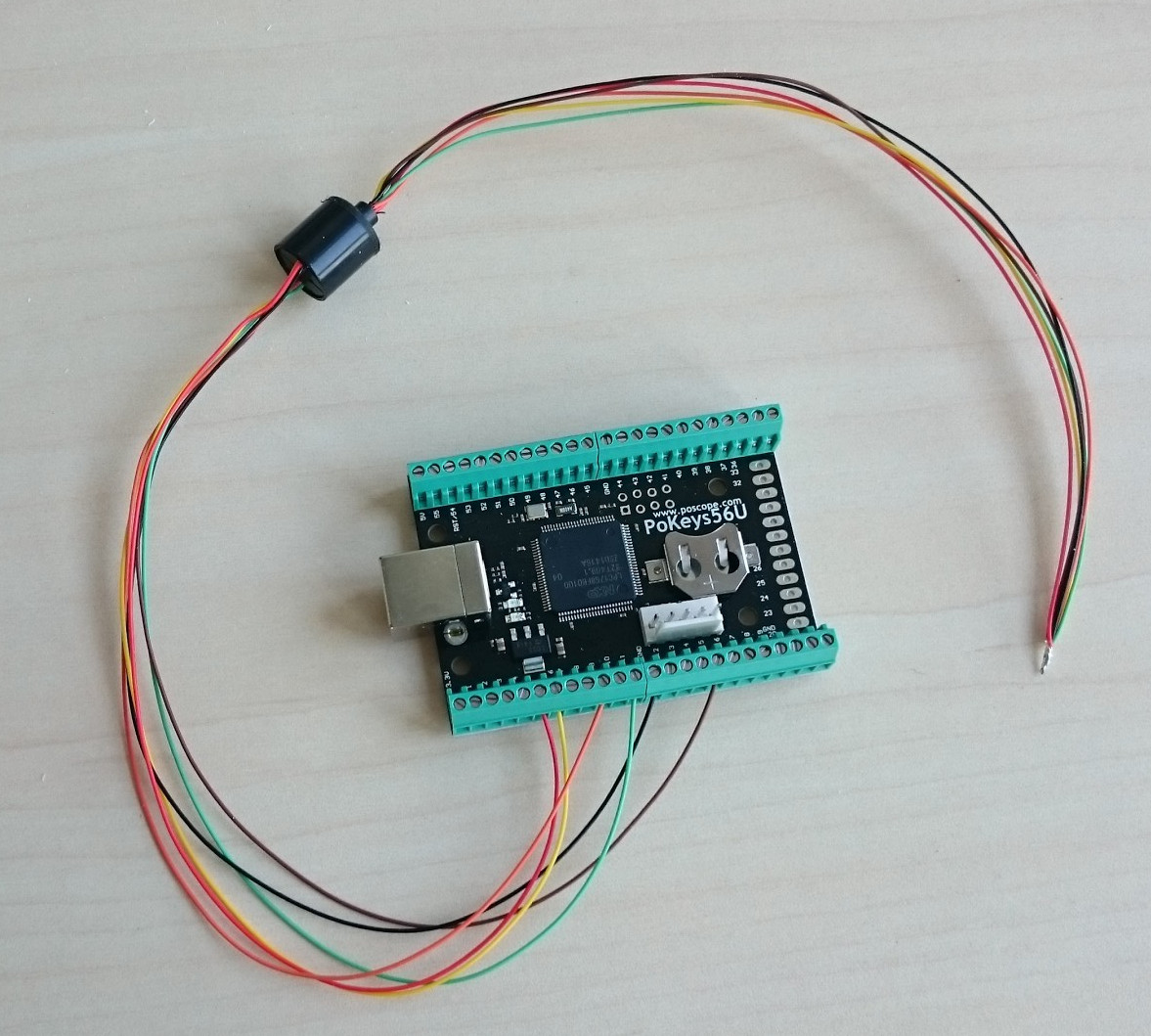
The PoKeys57U also benefits from slip ring tests when integrated into automated systems. This device, often used for motion control, can connect with various machinery and systems, including those that require continuous rotation. The PoKeys57U can manage inputs and outputs for different machine parts, but without reliable slip rings, even the most advanced control systems would struggle to maintain consistent performance. By conducting regular slip ring tests, operators can ensure that the PoKeys57U continues to function optimally, with minimal interruptions to the motion control and data transmission needed for seamless automation.
Slip ring tests are particularly important in high-precision applications, where the smallest failure can lead to significant problems. In industries such as aerospace, defense, and advanced manufacturing, even minor disruptions in signal or power flow can result in defects in the finished product, jeopardizing safety or operational efficiency. For example, in aerospace manufacturing, slip rings are used to ensure that rotating sensors and equipment continue to transmit data during flight simulations or testing. Testing the slip rings in these systems is critical to preventing costly errors, ensuring the safety and accuracy of the entire process.
Additionally, slip ring tests help assess the maintenance needs of the equipment, giving operators a proactive approach to machine care. Through regular testing, it’s possible to predict when a slip ring will require cleaning, lubrication, or replacement, reducing the likelihood of unexpected downtime. This proactive maintenance approach contributes to a more efficient operation, extending the lifespan of the slip ring and preventing potential failures that could result in costly repairs or production delays.
Overall, slip ring tests play a critical role in ensuring the reliability and performance of rotating components in automated systems. They ensure that the transfer of electrical power and signals remains uninterrupted and efficient, which is especially important in systems like CNC machines and robotic automation, where precision and consistency are key. Regular slip ring testing is an essential part of maintaining these systems, providing early warnings of potential issues and helping to extend the operational lifespan of valuable equipment. For industries relying on continuous motion and precise control, such as aerospace, manufacturing, and robotics, slip ring tests are an indispensable aspect of automation maintenance that supports overall system reliability and performance.
- Understanding Relay Modules: Smart Relay, Arduino Driving Relay, Raspberry Pi Relay, and 8-Channel Relay Modules
- A Comprehensive Guide to DAQ Devices, Raspberry Pi Temperature Loggers, RC Simulator Interfaces, and Ethernet I/O Controllers
Conclusion
In the world of modern engineering, precision and automation have become the cornerstones of progress. From the intricate control of CNC machines to the enhanced capabilities offered by devices like the PoKeys57U, technological advancements are continuously shaping how industries and hobbyists approach complex tasks. The integration of CNC controllers with automation systems has revolutionized manufacturing, enabling highly accurate and efficient production processes. Likewise, the PoKeys57U has emerged as a key enabler of advanced control, providing seamless connectivity, scalability, and versatility to both industrial and hobbyist applications, including the fascinating field of model railway automation.
Model railway enthusiasts, once limited by manual operations, now have the ability to create dynamic and lifelike setups through automation. The combination of CNC controllers, PoKeys57U, and other automation tools allows for the control of train movements, station management, and even the timing of light changes, adding layers of realism and interactivity to the model railway experience. This shift from simple manual control to sophisticated automation mirrors the broader trend in industries toward more efficient and precise operations.
However, as technology advances, maintaining the reliability of automated systems becomes increasingly crucial. Slip ring tests play a pivotal role in this regard, ensuring that essential rotating components in machinery, like CNC machines and robotic systems, continue to function smoothly and efficiently. By regularly testing slip rings, industries can prevent malfunctions, reduce downtime, and prolong the lifespan of critical equipment. In an era where automation is integral to both industrial and hobbyist sectors, ensuring the smooth operation of these systems through preventive maintenance is vital for continued success.
Ultimately, the convergence of CNC controllers, PoKeys57U, model railway automation, and slip ring tests illustrates how innovation in automation is transforming industries and enhancing our ability to create complex, efficient systems. Whether in large-scale manufacturing, cutting-edge robotics, or even model railroads, these technologies offer the precision, reliability, and flexibility needed to meet the growing demands of modern automation. As we continue to push the boundaries of what’s possible, these tools will remain integral to driving progress, ensuring that the future of engineering is not only more automated but also more connected, precise, and efficient.