In today’s rapidly advancing technological landscape, Computer Numerical Control (CNC) systems are more integral than ever in industrial and personal manufacturing settings. These machines automate complex processes, enhancing precision and efficiency in various applications. The modern CNC ecosystem consists of several critical components that work in tandem to deliver seamless operations. Among these are the Ethernet I/O controllers, Mach4 CNC controllers, Mach4 lasers, and CNC wiring. Understanding how each of these elements functions and interconnects is essential for anyone involved in CNC machining.
Ethernet I/O controllers are pivotal in facilitating communication between different CNC components, ensuring data is accurately relayed to drive machine operations. These controllers act as the nervous system of CNC setups, providing real-time input and output data exchange, which is crucial for precise machining tasks.
The Mach4 CNC controller represents a significant advancement in CNC software. It offers a customizable platform that supports various machine types, from routers and mills to lathes and lasers. Mach4’s flexibility and power make it a popular choice for both hobbyists and professionals looking to optimize their CNC machinery’s performance.
With the integration of Mach4 lasers, users can achieve unmatched precision in cutting and engraving tasks. These lasers expand the functionality of CNC machines, allowing for intricate designs and high-quality finishes on materials ranging from metals to plastics. The synergy between Mach4 software and laser technology is a game-changer in fields that demand exacting detail and minimal tolerances.
Lastly, CNC wiring is the unsung hero of any CNC setup. Proper wiring ensures stable connections and reliable power distribution, which are essential for the consistent operation of CNC machines. A well-wired CNC system minimizes downtime and maximizes productivity, making it a cornerstone of efficient manufacturing.
This article will delve into each of these components, exploring their roles and connections within the CNC ecosystem. By understanding the interplay between Ethernet I/O controllers, Mach4 CNC controllers, Mach4 lasers, and CNC wiring, you’ll gain insights into optimizing CNC systems for superior performance and reliability.
Understanding Ethernet I/O Controllers in CNC Systems
Ethernet I/O controllers have revolutionized the way CNC systems operate by providing an efficient and robust method for managing input and output signals. These controllers are crucial for facilitating communication between different components of CNC machinery, ensuring seamless data exchange that drives precise machining operations. In this section, we will explore the significance of Ethernet I/O controllers, their functionality, and their impact on modern CNC systems.
The Role of Ethernet I/O Controllers
Ethernet I/O controllers serve as the central hub for signal processing and data transmission in CNC machines. They are responsible for receiving input signals from various sensors and sending output signals to actuators and other machine components. This ensures that each part of the CNC system communicates effectively, leading to accurate and coordinated actions. With the rise of Industry 4.0, the demand for smarter and more connected manufacturing systems has made Ethernet I/O controllers an essential component in CNC setups.
Key Features of Ethernet I/O Controllers
- High-Speed Communication: Ethernet I/O controllers facilitate high-speed data transfer, allowing for real-time monitoring and control of CNC operations. This speed is critical for maintaining precision and reducing latency, especially in complex machining tasks.
- Scalability and Flexibility: One of the significant advantages of Ethernet I/O controllers is their scalability. They can easily integrate into existing CNC systems, supporting various configurations and expansions as needed. This flexibility makes them suitable for a wide range of applications, from small workshops to large-scale industrial operations.
- Remote Monitoring and Control: With Ethernet connectivity, these controllers enable remote monitoring and control of CNC systems. This capability allows operators to access machine data, perform diagnostics, and make adjustments from virtually anywhere, enhancing convenience and operational efficiency.
Benefits of Ethernet I/O Controllers in CNC Systems
Ethernet I/O controllers offer numerous benefits that contribute to the improved performance and reliability of CNC machines. By providing real-time data exchange, these controllers enable precise control over machining processes, reducing the likelihood of errors and material waste. Additionally, their scalability and remote capabilities allow for easy system upgrades and maintenance, ensuring that CNC setups remain up-to-date with the latest technological advancements.
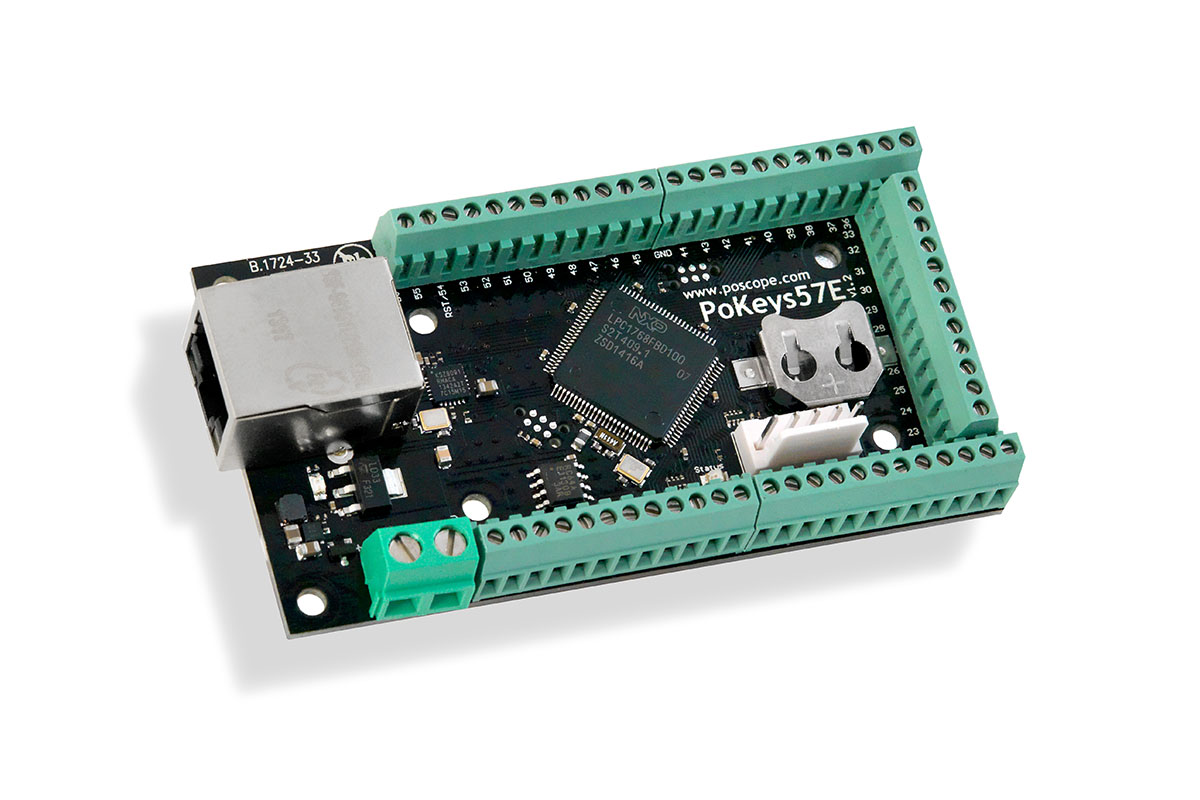
Moreover, Ethernet I/O controllers enhance the overall efficiency of CNC operations by streamlining communication between components. This streamlined communication results in faster machine response times, increased productivity, and reduced downtime, which are essential factors for maintaining competitive advantage in today’s manufacturing landscape.
Integration with Other CNC Components
The integration of Ethernet I/O controllers with other CNC components, such as Mach4 CNC controllers, further amplifies their benefits. Mach4 CNC controllers, known for their customizable and versatile nature, can work seamlessly with Ethernet I/O controllers to create a robust and efficient CNC system. This synergy allows for enhanced functionality and precision, catering to the diverse needs of modern machining applications.
In conclusion, Ethernet I/O controllers play a pivotal role in the advancement of CNC technology. Their ability to provide high-speed communication, scalability, and remote monitoring capabilities make them indispensable in today’s CNC systems. By understanding their functions and benefits, CNC operators and manufacturers can harness the full potential of these controllers to achieve superior machining performance and reliability.
Mach4 CNC Controller: A New Era in Precision Machining
The Mach4 CNC controller stands as a pivotal advancement in the world of computer numerical control, offering a highly customizable platform that enhances the capabilities of CNC machines. Designed for both hobbyists and industrial applications, Mach4 CNC controller software provides unparalleled flexibility and precision, making it a preferred choice for CNC enthusiasts and professionals alike. In this chapter, we will explore the features, benefits, and applications of the Mach4 CNC controller and how it contributes to the evolution of CNC technology.
Key Features of the Mach4 CNC Controller
- Customizability: One of the standout features of the Mach4 CNC controller is its high degree of customizability. Users can tailor the software to meet specific machining needs, from setting up custom tool paths to designing unique interfaces. This flexibility allows for the creation of bespoke solutions that can adapt to various CNC machines, whether they are routers, mills, lathes, or lasers.
- Advanced Motion Control: Mach4 provides advanced motion control capabilities that ensure smooth and precise movements during machining processes. The software supports multi-axis motion, allowing for intricate operations that require complex tool paths and precise cuts. This level of control is crucial for achieving high-quality finishes and maintaining tight tolerances in manufacturing.
- User-Friendly Interface: Despite its powerful features, the Mach4 CNC controller boasts a user-friendly interface that simplifies operation for both beginners and experienced machinists. The intuitive design allows users to easily navigate the software, access key functionalities, and monitor machining processes in real-time, reducing the learning curve and enhancing productivity.
- Versatility Across Applications: The Mach4 CNC controller is versatile enough to be used in a wide range of applications. Whether it’s woodworking, metalworking, or even laser cutting, Mach4 provides the necessary tools and features to handle diverse materials and processes. This versatility makes it an invaluable asset in both small-scale workshops and large manufacturing facilities.
Benefits of Using Mach4 CNC Controller
The Mach4 CNC controller offers numerous benefits that enhance the performance and efficiency of CNC systems. One of the primary advantages is its ability to improve machining accuracy. With its advanced motion control features, Mach4 ensures that every cut, engrave, or carve is executed with precision, reducing material waste and minimizing errors. This accuracy is particularly important in industries such as aerospace, automotive, and electronics, where even the slightest deviation can have significant implications.
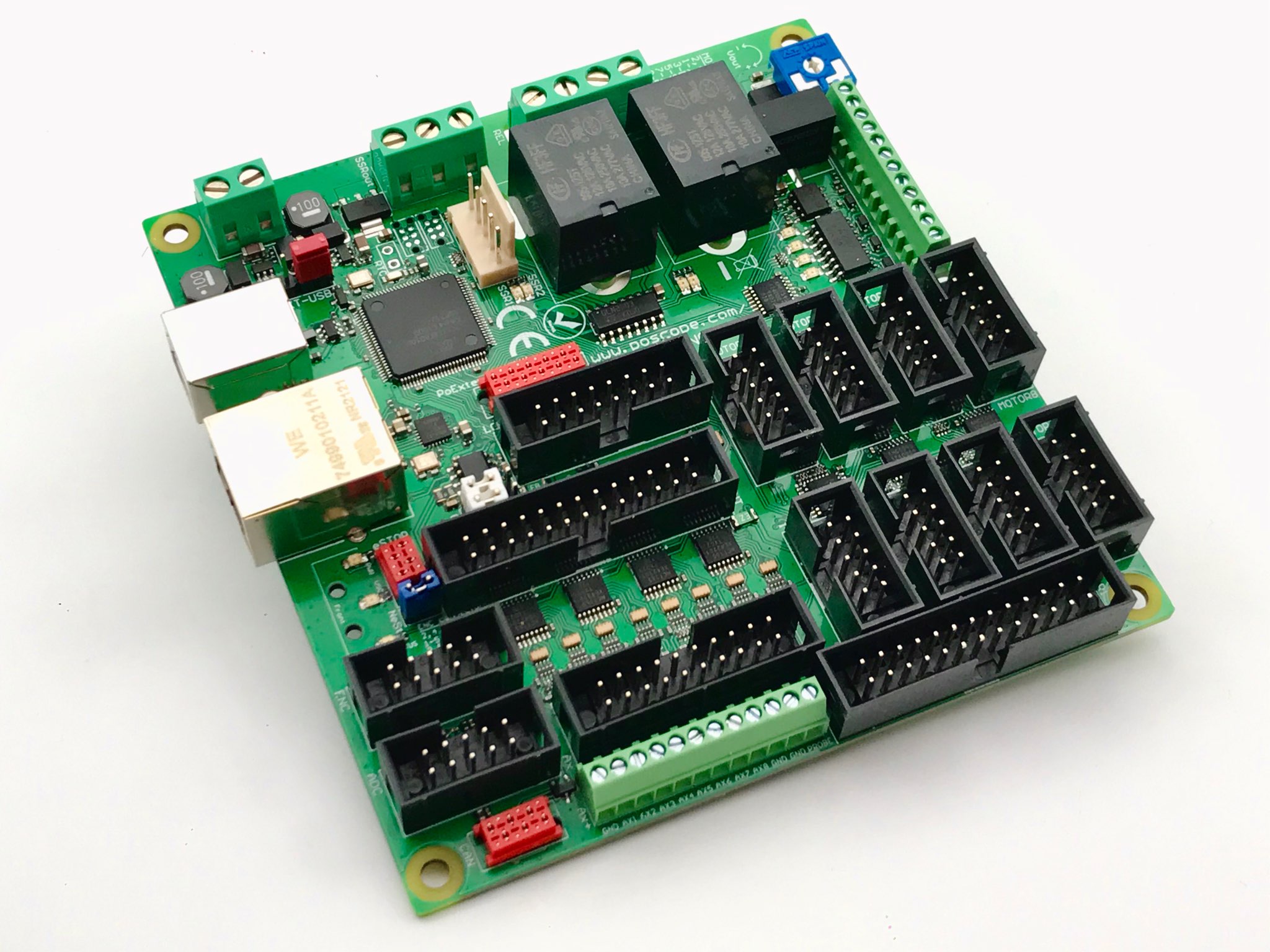
Moreover, the Mach4 CNC controller supports automation, enabling users to automate repetitive tasks and streamline workflows. By reducing manual intervention, Mach4 not only increases productivity but also minimizes the risk of human error, leading to more consistent and reliable outcomes. This automation capability is a game-changer for manufacturers looking to optimize production processes and maintain competitive advantage.
Another significant benefit of the Mach4 CNC controller is its integration capabilities. The software can easily integrate with various hardware components, including Ethernet I/O controllers, creating a cohesive and efficient CNC system. This integration allows for seamless communication between components, enhancing overall system performance and reliability.
Applications of the Mach4 CNC Controller
The versatility and advanced features of the Mach4 CNC controller make it suitable for a wide range of applications. In the woodworking industry, Mach4 is used to create intricate designs and patterns, from cabinetry to decorative carvings. The software’s precision and control ensure that even the most complex designs are executed flawlessly, resulting in high-quality finished products.
In metalworking, the Mach4 CNC controller facilitates the machining of metal parts with high precision and speed. It supports complex tool paths and multi-axis operations, allowing for the production of intricate components used in various industries, such as automotive and aerospace. Mach4’s advanced motion control ensures that metal parts are machined with tight tolerances, meeting the stringent quality standards of these industries.
Additionally, the Mach4 CNC controller is widely used in laser cutting and engraving applications. When combined with Mach4 lasers, the software provides unmatched precision and control, enabling users to create detailed engravings and cuts on a variety of materials. This capability is particularly valuable in industries such as signage, jewelry, and electronics, where intricate designs and fine details are essential.
The Mach4 CNC controller is a powerful tool that significantly enhances the capabilities of CNC machines. Its customizability, advanced motion control, user-friendly interface, and versatility across applications make it an essential component in modern CNC systems. By providing precise control and integration capabilities, the Mach4 CNC controller enables users to optimize machining processes, improve productivity, and achieve superior results. Whether you’re a hobbyist or a professional manufacturer, understanding the features and benefits of the Mach4 CNC controller can help you unlock the full potential of your CNC machine.
Harnessing Precision with Mach4 Lasers: A Deep Dive into CNC Laser Applications
Mach4 lasers represent a cutting-edge advancement in CNC technology, offering exceptional precision and control for cutting, engraving, and marking applications. As CNC machines continue to evolve, the integration of laser technology has opened new possibilities for industries requiring intricate designs and high-quality finishes. In this chapter, we will explore the capabilities of Mach4 lasers, their applications, and how they enhance CNC systems by providing unmatched precision and efficiency.
Key Features of Mach4 Lasers
- Unmatched Precision: One of the most significant advantages of Mach4 lasers is their unparalleled precision. These lasers are capable of executing intricate cuts and engravings with micron-level accuracy, making them ideal for applications requiring detailed work. Whether it’s cutting complex shapes or engraving fine patterns, Mach4 lasers ensure every task is performed with the highest level of precision.
- Versatility Across Materials: Mach4 lasers are designed to work with a wide range of materials, from metals and plastics to wood and glass. This versatility allows users to tackle diverse projects, whether they’re crafting intricate jewelry designs, creating detailed signage, or cutting precise components for electronics. The ability to seamlessly switch between different materials makes Mach4 lasers a valuable asset in any CNC setup.
- High-Speed Operation: Efficiency is a hallmark of Mach4 lasers. These lasers are engineered for high-speed operation, enabling faster cutting and engraving without compromising quality. This speed is particularly beneficial in production environments where time is critical, as it allows for quicker turnaround times and increased throughput.
- User-Friendly Interface: Despite their advanced capabilities, Mach4 lasers maintain a user-friendly interface that simplifies operation. Users can easily program laser paths, adjust settings, and monitor progress, making it accessible even for those new to CNC laser technology. This intuitive design ensures that operators can focus on the creative and technical aspects of their work rather than getting bogged down by complex controls.
Benefits of Using Mach4 Lasers in CNC Applications
Integrating Mach4 lasers into CNC systems provides numerous benefits that enhance overall machining performance. One of the primary advantages is the ability to achieve clean and precise cuts with minimal material waste. Unlike traditional cutting methods, laser technology reduces the need for physical contact, resulting in smoother edges and less debris. This precision minimizes post-processing requirements, saving both time and resources.
Additionally, Mach4 lasers offer the flexibility to work with various materials without needing frequent tool changes. This adaptability not only streamlines operations but also reduces downtime associated with manual adjustments. By seamlessly transitioning between materials, manufacturers can optimize workflow efficiency and maintain consistent production quality.
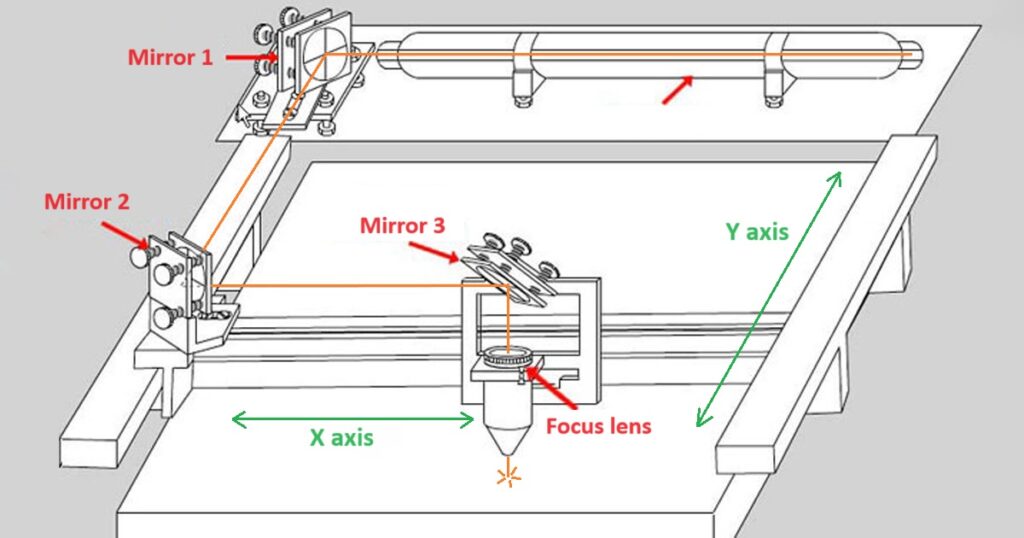
Another significant benefit of Mach4 lasers is their ability to create intricate designs that are difficult or impossible to achieve with other methods. From delicate engravings on fine jewelry to complex patterns on architectural models, these lasers provide the precision needed to bring artistic and technical visions to life. This capability is invaluable in industries such as fashion, art, and architecture, where unique designs and craftsmanship are paramount.
Applications of Mach4 Lasers
Mach4 lasers find applications in a wide array of industries, each benefiting from the technology’s precision and versatility. In the jewelry industry, for example, laser engraving is used to add intricate details to rings, necklaces, and other pieces, enhancing their aesthetic appeal and value. The precision of Mach4 lasers allows jewelers to execute delicate designs with ease, ensuring high-quality results.
In the signage industry, Mach4 lasers enable the creation of detailed and durable signs with crisp text and sharp images. Whether working with acrylic, wood, or metal, these lasers produce clean cuts and engravings that stand out, making them ideal for businesses seeking to create eye-catching signage.
The electronics industry also benefits significantly from Mach4 laser technology. With the ability to cut and engrave circuit boards and components with micron-level precision, Mach4 lasers play a crucial role in the production of electronic devices. Their accuracy ensures that components fit together perfectly, reducing the risk of defects and improving the reliability of finished products.
Additionally, the art and architecture industries have embraced Mach4 lasers for their ability to produce detailed models and sculptures. Artists and architects can use these lasers to create complex structures and intricate patterns, pushing the boundaries of design and creativity. This technology enables the realization of innovative concepts that were once difficult to achieve with traditional methods.
Integration with CNC Systems
The integration of Mach4 lasers with CNC systems enhances the overall capabilities of machining setups. By combining laser technology with CNC machinery, users gain the ability to execute a wide range of tasks, from cutting and engraving to marking and sculpting. This integration allows for a more comprehensive approach to manufacturing, enabling users to tackle diverse projects with a single system.
When paired with the Mach4 CNC controller, Mach4 lasers offer even greater precision and control. The software’s advanced motion control capabilities ensure that laser paths are executed with accuracy, resulting in high-quality finishes and minimal material waste. Additionally, the synergy between Mach4 lasers and CNC wiring ensures stable connections and reliable power distribution, further enhancing system performance and efficiency.
Mach4 lasers represent a transformative advancement in CNC technology, providing unmatched precision, versatility, and efficiency across various applications. Their ability to execute intricate designs and cuts with high-speed operation makes them an invaluable tool for industries ranging from jewelry and signage to electronics and architecture. By integrating Mach4 lasers with CNC systems, users can unlock new possibilities in manufacturing, achieving superior results and pushing the boundaries of creativity. Understanding the features and benefits of Mach4 lasers is essential for anyone looking to optimize their CNC operations and stay ahead in today’s competitive market.
Mastering CNC Wiring: The Backbone of Efficient CNC Systems
CNC wiring is an often overlooked yet crucial component of CNC systems, playing a vital role in ensuring seamless operation and performance. The wiring in a CNC machine forms the physical connections that link various components, enabling them to communicate and function effectively. Proper CNC wiring not only guarantees reliable power distribution and data transfer but also minimizes potential issues such as signal interference and electrical faults. In this chapter, we will explore the fundamentals of CNC wiring, its importance, and best practices to optimize CNC system performance.
The Importance of CNC Wiring
CNC wiring serves as the backbone of any CNC machine, providing the necessary electrical pathways that connect the machine’s control unit, motors, sensors, and other peripherals. Without proper wiring, even the most advanced CNC components, like the Mach4 CNC controller and Ethernet I/O controllers, cannot function correctly. As such, the quality and configuration of CNC wiring directly impact the overall efficiency, reliability, and safety of the entire system.
Key Components of CNC Wiring
- Power Supply Wires: Power supply wires are responsible for delivering electricity from the power source to various components within the CNC machine. They must be appropriately sized and insulated to handle the electrical load and prevent overheating or electrical shorts. Ensuring a stable power supply is critical for maintaining consistent machine performance and preventing unexpected shutdowns.
- Signal Wires: Signal wires transmit data between the CNC controller and machine components, such as motors, sensors, and Ethernet I/O controllers. These wires must be shielded to protect against electromagnetic interference (EMI), which can disrupt signal integrity and lead to malfunctions. High-quality signal wiring is essential for accurate data transfer and precise machine operation.
- Grounding Wires: Grounding wires play a crucial role in safety by providing a path for electrical current to dissipate in the event of a fault. Proper grounding helps prevent electrical shock, equipment damage, and data corruption, ensuring the safety of operators and the longevity of the CNC system. All CNC machines should have a reliable grounding setup to mitigate risks associated with electrical faults.
- Motor and Encoder Cables: Motor and encoder cables are specifically designed to connect CNC motors and encoders to the control system. These cables must be flexible, durable, and resistant to wear, as they often endure constant movement and vibration during machine operation. Using high-quality motor and encoder cables ensures accurate motion control and feedback, essential for maintaining machining precision.
Best Practices for CNC Wiring
Implementing best practices in CNC wiring is critical to optimize system performance and prevent potential issues. Here are some key guidelines to follow:
- Use the Right Cable Types and Sizes: Selecting the appropriate cable type and size for each application is essential for maintaining efficient electrical flow. Power cables should be capable of handling the machine’s current requirements, while signal cables should be shielded to protect against EMI. Overloading cables can lead to overheating and equipment failure, so it’s crucial to follow manufacturer recommendations.
- Proper Cable Routing: Proper cable routing involves organizing cables in a manner that minimizes interference and wear. Cables should be routed away from heat sources and moving parts to prevent damage. Using cable trays, conduits, and ties can help keep cables organized and secure, reducing the risk of accidental disconnection or damage during machine operation.
- Ensure Proper Grounding: As mentioned earlier, grounding is vital for safety and reliability. Ensure all components are adequately grounded to prevent electrical faults. Regularly inspect grounding connections for corrosion or looseness, and address any issues promptly to maintain system safety.
- Regular Maintenance and Inspections: Routine maintenance and inspections of CNC wiring can help identify potential problems before they escalate. Check for signs of wear, fraying, or damage to cables, and replace any compromised wiring immediately. Periodic inspections can prevent costly downtime and extend the lifespan of the CNC machine.
- Labeling and Documentation: Proper labeling and documentation of CNC wiring simplify troubleshooting and maintenance. Clearly label all wires and connections, and keep detailed records of the wiring layout and any modifications made. This practice helps technicians quickly identify and address issues, reducing machine downtime and maintenance costs.
- Use Quality Connectors: High-quality connectors are essential for ensuring reliable electrical connections. Poor-quality connectors can lead to loose connections, electrical resistance, and signal loss, negatively impacting machine performance. Invest in durable connectors that provide secure and stable connections to maintain optimal system functionality.
Common CNC Wiring Challenges and Solutions
While proper CNC wiring can enhance system performance, several challenges can arise that require attention:
- Electromagnetic Interference (EMI): EMI can disrupt data transmission, leading to errors and inaccuracies in CNC operations. To combat EMI, use shielded cables and separate power and signal wires to minimize cross-interference. Additionally, maintaining proper grounding can help reduce the impact of EMI on the system.
- Cable Wear and Tear: Constant movement and vibration in CNC machines can lead to cable wear and tear. Regularly inspect cables for signs of damage, and use flexible, durable cables designed for motion-intensive applications. Implementing cable management solutions, such as cable carriers, can also help protect cables from excessive wear.
- Inadequate Power Supply: Insufficient power supply can cause machine instability and unexpected shutdowns. Ensure power supply wires are correctly sized and capable of handling the machine’s electrical load. Consider installing uninterruptible power supplies (UPS) to provide backup power and prevent disruptions during outages.
- Heat and Environmental Factors: High temperatures and environmental factors can affect CNC wiring integrity. Use heat-resistant cables and proper insulation to protect against temperature fluctuations. Additionally, keep the CNC machine in a controlled environment to minimize exposure to dust, moisture, and other harmful elements.
Integration of CNC Wiring with CNC Systems
The integration of CNC wiring with CNC systems is fundamental to achieving seamless operation and enhancing overall machine performance. By ensuring proper electrical connections and data transmission, CNC wiring supports the functionality of advanced components such as Ethernet I/O controllers, Mach4 CNC controllers, and Mach4 lasers.
When integrated with these components, CNC wiring enables efficient communication and coordination within the system, resulting in improved accuracy, reliability, and productivity. For instance, Ethernet I/O controllers rely on precise wiring to transmit data between sensors and actuators, while the Mach4 CNC controller requires reliable connections to execute complex motion control tasks. Additionally, Mach4 lasers depend on stable power and signal pathways to perform intricate cutting and engraving operations with precision.
CNC wiring is a critical aspect of CNC systems, serving as the foundation for efficient and reliable machine operation. By providing stable electrical connections and facilitating seamless communication between components, proper CNC wiring ensures the performance and longevity of CNC machines. Understanding the key components, best practices, and common challenges of CNC wiring empowers operators and manufacturers to optimize their CNC systems for superior results. Whether you’re setting up a new CNC machine or maintaining an existing one, investing in quality wiring and adhering to best practices is essential for achieving optimal performance and minimizing downtime.
Conclusion
In the ever-evolving realm of CNC technology, the integration and optimization of key components such as Ethernet I/O controllers, Mach4 CNC controllers, Mach4 lasers, and CNC wiring are fundamental to achieving superior performance and reliability. Each of these elements plays a crucial role in enhancing the capabilities and efficiency of CNC systems.
Ethernet I/O controllers serve as the communication backbone, ensuring seamless data exchange between different machine components and enabling real-time monitoring and control. Their high-speed communication and flexibility make them indispensable for maintaining precise and efficient CNC operations.
The Mach4 CNC controller brings a new level of versatility and precision to CNC machining. Its customizability and advanced motion control capabilities allow users to tailor their CNC systems to meet specific needs, whether for hobbyist projects or complex industrial applications. The ability to automate and optimize various machining processes further enhances productivity and accuracy.
Mach4 lasers offer unmatched precision and speed for cutting, engraving, and marking across a wide range of materials. Their integration with CNC systems enables the creation of intricate designs and high-quality finishes, making them a valuable tool in industries such as jewelry, signage, electronics, and art.
Lastly, CNC wiring is the critical infrastructure that supports the operation of these advanced components. Proper wiring ensures reliable power distribution, accurate signal transmission, and effective grounding, all of which contribute to the overall stability and efficiency of CNC machines. Adhering to best practices in wiring not only prevents potential issues but also maximizes system performance and longevity.
By understanding and effectively integrating these components, CNC operators and manufacturers can unlock the full potential of their systems, leading to enhanced precision, productivity, and quality. Whether you’re setting up a new CNC machine or optimizing an existing one, a comprehensive grasp of Ethernet I/O controllers, Mach4 CNC controllers, Mach4 lasers, and CNC wiring is essential for staying at the forefront of CNC technology. Embracing these advancements and adhering to best practices will ensure that your CNC operations are efficient, reliable, and capable of meeting the demands of today’s competitive manufacturing landscape.