In today’s rapidly advancing industrial landscape, automation plays a crucial role in increasing efficiency, precision, and productivity. From manufacturing plants to sophisticated robotics, automation technology has become the backbone of modern industry. Key components like Ethernet I/O controllers, Modbus stepper drivers, stepper motor currents, and automation control devices form the essential building blocks of these automated systems.
This article aims to demystify these crucial components, exploring how each part functions individually and how they work together to create a cohesive and efficient automated system. Understanding these elements is vital for engineers, technicians, and enthusiasts looking to optimize their operations or dive into the world of industrial automation.
We’ll begin by delving into the Ethernet I/O controller, a pivotal piece of hardware that enables seamless communication between various devices in an automation network. Next, we’ll explore the Modbus stepper driver, a key component for controlling stepper motors, which are integral to precise movement and positioning tasks. We’ll then examine the stepper motor current, a fundamental aspect that determines the performance and efficiency of stepper motors. Finally, we’ll look into the broader category of automation control devices, which orchestrate the entire automation process, ensuring that all components work harmoniously together.
Whether you’re an automation veteran or new to the field, understanding these technologies will provide valuable insights into how modern industrial systems operate and how they can be improved for optimal performance. Let’s dive in and explore the intricacies of these essential components that make automation possible.
Ethernet I/O Controller
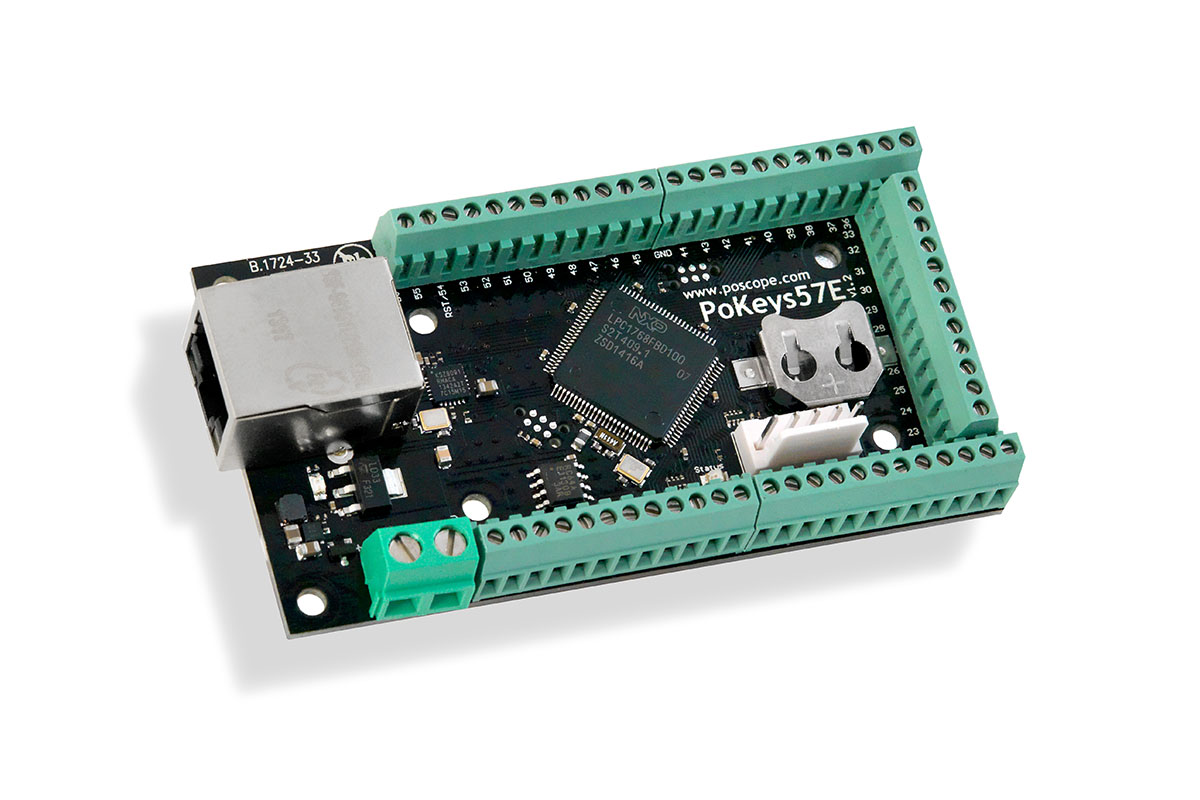
In the realm of industrial automation, the Ethernet I/O controller is a vital component that facilitates communication between various devices within a network. It serves as the bridge between input/output signals and a central processing system, allowing for seamless data exchange. By employing Ethernet technology, these controllers enable fast and reliable data transmission, which is essential for real-time decision-making in automated processes.
One of the primary advantages of an Ethernet I/O controller is its ability to handle large volumes of data over long distances with minimal latency. This capability makes it ideal for complex automation systems where multiple devices need to interact efficiently. Unlike traditional serial connections, Ethernet offers high-speed communication that can support a wide array of applications, from simple sensor monitoring to complex robotic operations.
Additionally, the Ethernet I/O controller is known for its scalability and flexibility. Manufacturers can easily expand their automation systems by integrating additional devices without the need for significant infrastructure changes. This flexibility is crucial in industries where processes are continually evolving, and adaptability is a key factor in maintaining competitive advantage.
Security is another critical feature of the Ethernet I/O controller. With industrial systems increasingly being targeted by cyber threats, Ethernet controllers are equipped with advanced security protocols to protect sensitive data and ensure system integrity. Encryption and authentication measures are typically employed to safeguard communication between devices, making them a reliable choice for modern industrial environments.
The integration of Ethernet technology into I/O controllers has revolutionized the way automation systems operate, providing unmatched speed, reliability, and security. Whether in manufacturing, logistics, or any industry reliant on automation, the Ethernet I/O controller is an indispensable tool that enhances both performance and efficiency.
Modbus Stepper Driver
In the field of automation, the Modbus stepper driver is a critical component for precise motor control. Stepper motors are widely used in various applications requiring accurate positioning and control, and the Modbus stepper driver plays a crucial role in this process. It acts as an interface between the control system and the stepper motor, translating digital commands into precise motor movements.
The Modbus protocol, a widely used communication protocol in industrial environments, is integral to the operation of these drivers. It allows multiple devices to communicate efficiently over a network, providing a standardized method for transmitting data. The Modbus stepper driver leverages this protocol to ensure accurate control and synchronization of stepper motors across different devices and applications.
One of the main benefits of using a Modbus stepper driver is its ability to provide precise control over motor speed and position. By utilizing the Modbus protocol, these drivers can send detailed instructions to the stepper motor, allowing for smooth and accurate movement. This level of precision is essential in applications such as CNC machines, 3D printers, and robotic arms, where even minor deviations can lead to significant errors.
Additionally, the Modbus stepper driver supports a variety of configurations and settings, allowing users to customize motor behavior according to specific application requirements. Parameters such as acceleration, deceleration, and torque can be adjusted, offering greater flexibility and control over motor operations.
The integration of the Modbus stepper driver into automation systems not only enhances motor control but also improves overall system efficiency. By enabling precise and synchronized motor movements, these drivers contribute to the seamless operation of complex automated processes, ensuring that tasks are executed with the highest level of accuracy.
Stepper Motor Current
When discussing the performance and efficiency of stepper motors, stepper motor current is a key factor that cannot be overlooked. The current supplied to a stepper motor directly influences its torque, speed, and overall performance, making it a critical aspect of motor control in automation systems.
The stepper motor current determines the magnetic field strength generated within the motor, which in turn affects the motor’s torque output. Higher currents generally result in greater torque, allowing the motor to handle heavier loads and achieve faster speeds. However, excessive current can lead to overheating and increased wear on the motor components, potentially reducing the motor’s lifespan.
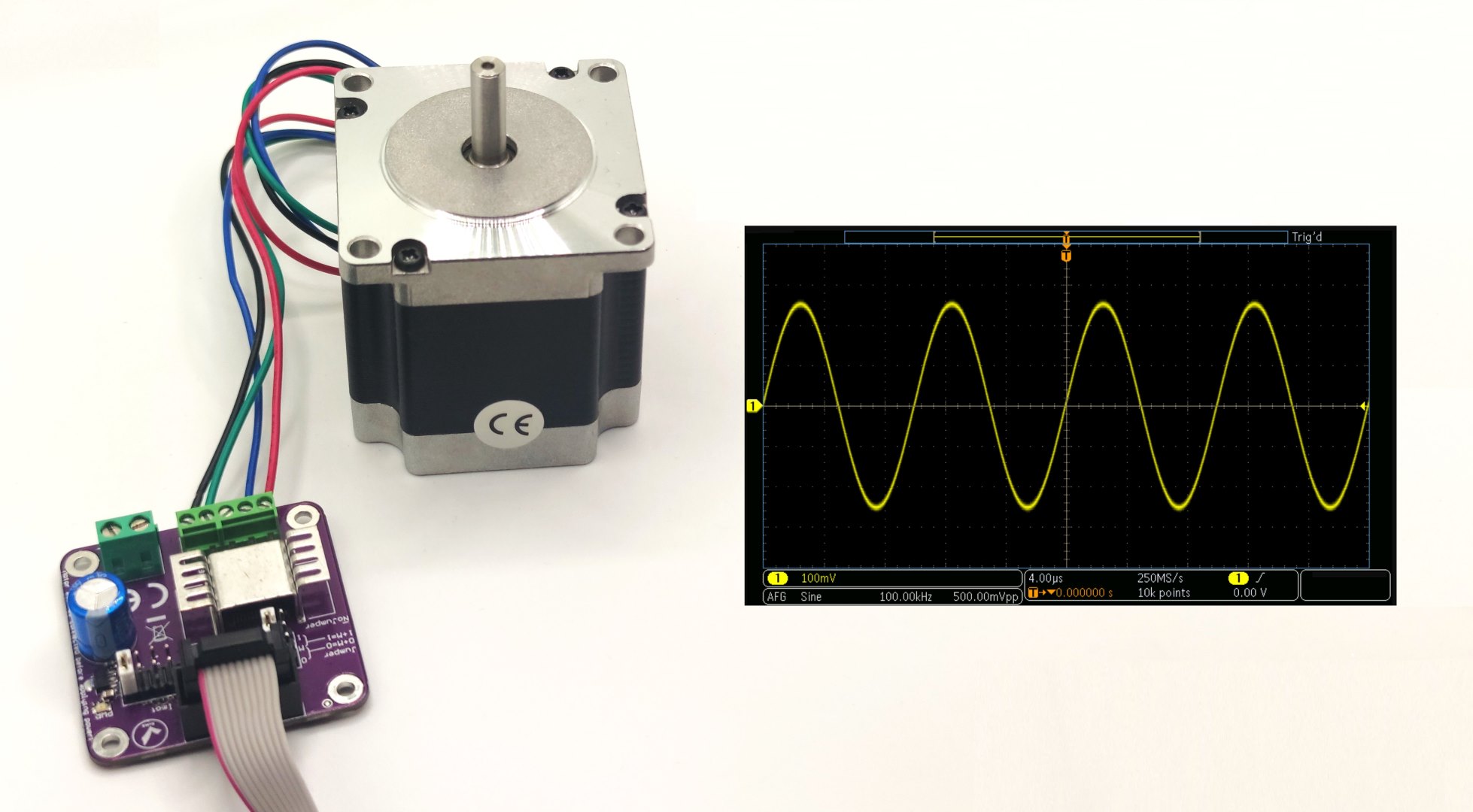
To optimize performance, it is essential to carefully manage the stepper motor current. Many modern stepper drivers offer current control features that allow users to adjust the current levels according to specific application needs. By fine-tuning the current, operators can achieve a balance between performance and energy efficiency, ensuring that the motor operates within safe parameters while delivering the required torque and speed.
Another important consideration is the relationship between stepper motor current and heat generation. As current flows through the motor windings, it generates heat, which must be dissipated to prevent damage. Effective thermal management, including the use of heat sinks and cooling systems, is crucial in maintaining optimal motor performance and extending its operational life.
Moreover, stepper motor current plays a role in determining the motor’s holding torque, which is the ability to maintain a position when stationary. In applications requiring precise positioning, such as CNC machining and 3D printing, maintaining adequate holding torque is essential for ensuring accuracy and stability.
Understanding and controlling stepper motor current is vital for achieving optimal performance and longevity in automated systems. By carefully managing current levels, operators can enhance motor efficiency, reduce energy consumption, and ensure reliable operation in a wide range of industrial applications.
Automation Control Device
The automation control device is a central component in modern industrial systems, responsible for orchestrating the various elements of an automation process. These devices, which include programmable logic controllers (PLCs), human-machine interfaces (HMIs), and distributed control systems (DCS), provide the intelligence and coordination necessary for seamless operation of automated tasks.
At the heart of an automation control device is its ability to receive, process, and transmit data. These devices act as the brain of an automation system, collecting input from sensors and other field devices, processing this data to make informed decisions, and sending commands to actuators and other output devices. This capability enables real-time control and monitoring of complex processes, ensuring that operations run smoothly and efficiently.
One of the key features of an automation control device is its programmability. Users can create custom programs tailored to specific applications, allowing for precise control and automation of tasks. This flexibility is crucial in industries where processes vary widely, enabling operators to adapt systems to meet unique operational requirements.
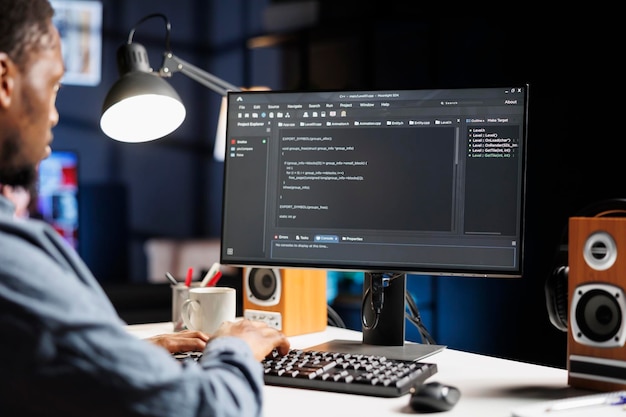
Moreover, the automation control device offers advanced diagnostic and monitoring capabilities. By continuously tracking system performance and identifying potential issues, these devices help prevent downtime and maintain productivity. Remote monitoring features also allow operators to oversee operations from anywhere, providing greater control and visibility over automated processes.
In addition to their control functions, automation control devices often integrate with other components such as Ethernet I/O controllers, Modbus stepper drivers, and stepper motors. This integration facilitates seamless communication and coordination between different parts of an automation system, enhancing overall efficiency and effectiveness.
As technology continues to evolve, automation control devices are becoming more sophisticated, incorporating features like machine learning and artificial intelligence to further improve decision-making and system optimization. These advancements are paving the way for smarter, more autonomous industrial systems that offer increased productivity and reduced operational costs.
Conclusion
In the world of industrial automation, understanding the core components like Ethernet I/O controllers, Modbus stepper drivers, stepper motor currents, and automation control devices is essential for optimizing performance and efficiency. These components work together to create cohesive systems that drive modern industry, offering unparalleled precision, control, and reliability.
The Ethernet I/O controller provides the communication backbone for automation networks, enabling fast and secure data exchange. The Modbus stepper driver ensures precise motor control, essential for accurate positioning and movement in various applications. Stepper motor current is a key factor in determining motor performance, influencing torque, speed, and energy efficiency. Finally, the automation control device orchestrates the entire process, offering programmability and advanced monitoring capabilities for seamless operation.
By understanding and leveraging these technologies, businesses can enhance their automation systems, achieve greater productivity, and stay competitive in an ever-evolving industrial landscape. Whether you’re involved in manufacturing, logistics, or any field relying on automation, these components are integral to achieving success in today’s fast-paced world.